Como ya vimos en el anterior artículo, el metanol está emergiendo como una pieza clave en la transición hacia un futuro más sostenible en diversos sectores, incluido el transporte y, de manera destacada, el sector marítimo. Con el aumento de las exigencias regulatorias y la necesidad de reducir las emisiones de CO₂, el e-metanol se posiciona como una alternativa viable a los combustibles tradicionales. Este combustible sintético, considerado un tipo de RFNBO (Renewable Fuels of Non-Biological Origin), se produce utilizando H2, producido a partir de electricidad renovable junto con recursos como el agua, y dióxido de carbono (CO₂) capturado.
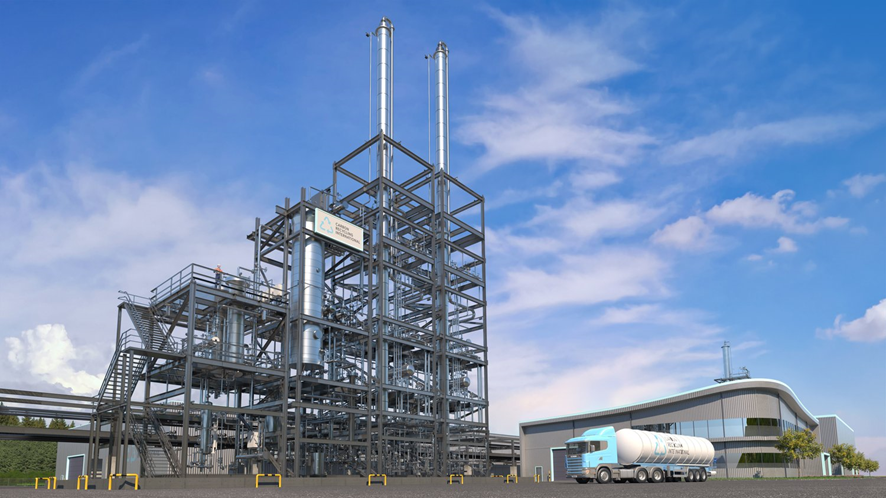
Ilustración 1 Planta de metanol ubicada en Islandia (capacidad 4.000 toneladas anuales).
Costes de Inversión
La principal barrera para la adopción del metanol renovable es la misma que para otros combustibles alternativos y materias primas renovables: el costo de producción. El desarrollo de plantas de producción de e-metanol conlleva una inversión significativa. Por ejemplo, una planta capaz de producir 60.000 toneladas al año puede suponer una inversión estimada de entre 70 – 90 millones de euros, sin contar la inversión de la planta de producción de hidrogeno.
En el proceso de producción de e-metanol, el hidrogeno y dióxido de carbono comprimidos se introducen en el reactor de producción de metanol, donde ocurre la hidrogenación del CO2 en presencia de un catalizador de cobre, zinc y aluminio. La reacción, que se realiza a altas presiones (40-100 bar) y temperaturas (200-300 °C), produce metanol crudo, compuesto por metanol y agua. Dado que la reacción es exotérmica, el calor generado se disipa utilizando agua como refrigerante, que se evapora, o mediante el enfriamiento de la mezcla de gases de entrada. Una vez obtenido el metanol crudo, este se dirige a un sistema de destilación donde se separan el metanol y el agua para obtener corrientes casi puras de ambos. El calor residual del reactor puede aprovecharse en esta etapa para reducir la energía externa necesaria en la destilación, optimizando el proceso energético (IRENA, Renewable Methanol Outlook, 2021)(Sollai, 2023).
De este modo, una planta de producción de metanol a partir de CO₂ e hidrógeno se asemeja a una planta química convencional en términos de infraestructura, procesos y equipos utilizados, como reactores, compresores y sistemas de control. Al igual que en la producción petroquímica tradicional, la síntesis de metanol involucra reacciones catalíticas a alta presión y temperatura, lo que permite aplicar principios de economía de escala. Esto significa que, a medida que aumenta la capacidad de producción de la planta, los costos unitarios de operación y capital se reducen significativamente, haciendo que la producción de metanol verde sea más competitiva y viable a gran escala.
Consumos e-metanol
El proceso de producción de e-metanol requiere la combinación de hidrógeno verde y dióxido de carbono capturado. En términos de insumos, se necesitan 0,2 toneladas de hidrógeno (H₂) y 1,4 toneladas de CO₂ para producir una tonelada de metanol.
En cuanto al consumo de utilities, el proceso de producción de e-metanol se traduce en un consumo de 0,8 MWh eléctricos, 0,23 MWh térmicos por tonelada de metanol y la necesidad de disipar 2 MW de calor por tonelada de metanol. A modo de ejemplo, la siguiente tabla muestra un caso base con las necesidades de materias primas y consumos de utilities estimados para una planta con una capacidad de 60.000 toneladas al año:
Tabla 1 Consumos estimados para una planta de 60 KTA de metanol.
Parámetro | Valor |
Consumo anual H2 (t) | 12.000 |
Consumo CO2 (t) | 84.000 |
Consumo eléctrico (MW) | 6 |
Demanda térmica (MWt) | 1,7 |
Demanda refrigeración (MWt) | 15 |
Es importante tener en cuenta que estos consumos son estimados y pueden variar dependiendo de las condiciones operativas, así como de la presión a la que se reciben el hidrógeno (H₂) y el dióxido de carbono (CO₂). En este caso de referencia, se asume que tanto el CO2 como el H2 llegan a presión atmosférica, por lo que el consumo energético de la planta es elevado debido a la necesidad de comprimir ambas corrientes. El consumo energético podría reducirse considerablemente si las materias primas se suministraran a una presión más cercana a la de operación.
Factores limitantes en el coste
La principal barrera para la adopción del metanol renovable es la misma que para otros combustibles alternativos y materias primas renovables: el costo de producción (IRENA, Renewable Methanol Outlook, 2021).
En el caso del e-methanol es importante destacar el papel crucial que juega el coste de producción de CO2 e H2 en la determinación del coste final del metanol. Para ejemplificar este concepto, considera únicamente la adquisición de materias primas asumiendo un coste de 4000 €/ton para el hidrógeno y 100 €/ton para el CO₂, el coste base del metanol sería de 940 €. Este es el coste base únicamente teniendo en cuenta el coste de las materias primas, el cual supone sobre un 80% del coste final del metanol.
En la siguiente imagen, se puede observar la variación del precio estimado del metanol en función del coste del hidrógeno y el CO₂. Esta relación es crucial para entender la competitividad de la producción del e-metanol.
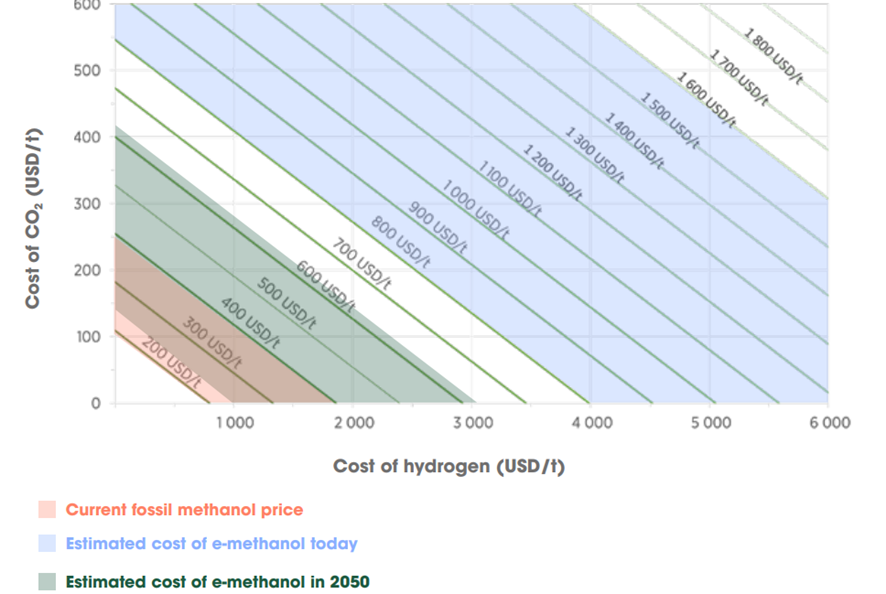
Ilustración 2 Coste del metanol en función del coste de H2 y CO2 (IRENA, Renewable Methanol Outlook, 2021).
De este modo, la principal barrera para la producción de e-metanol a partir de CO₂ e hidrógeno es su elevado coste, especialmente debido a la electrólisis del agua para producir hidrógeno, que consume alrededor de 55 MWh por tonelada de H₂. Por lo que, reducir el precio de la energía renovable es clave para bajar el precio actual del e-metanol a niveles más competitivos.
Estrategias de Integración de la planta metanol
Pureza del CO₂ y el Catalizador: Importancia y Efectos
Uno de los aspectos clave en la producción de metanol renovable es la pureza del CO₂. Para una conversión eficiente en metanol, el CO₂ debe minimizar sus contaminantes e impurezas, ya que podrían desactivar los catalizadores y reducir la eficiencia del proceso.
– Catalizadores y su sensibilidad: Los catalizadores típicos utilizados en la producción de metanol incluyen cobre, zinc y aluminio, y son sensibles a impurezas que interfieren con su actividad. La presencia de contaminantes puede envenenar los catalizadores, disminuyendo la tasa de conversión de CO₂ y afectando la productividad global de la planta.
– Impacto de los Inertes: Los gases inertes, como el nitrógeno o el argón, no participan en las reacciones de formación de metanol. Su presencia reduce la concentración de los reactivos (H₂ y CO₂) en la mezcla de reacción, lo que diluye el proceso, lo que puede provocar una menor interacción con los sitios activos del catalizador, y aumenta el consumo de energía por la necesidad de comprimir o reciclar mayores volúmenes de gases. De este modo, reducen la eficiencia energética global de la planta.
Para la planta de producción de metanol, se espera una pureza del CO2 del 99,6% mientras que se espera una pureza del H2 del 99,8%. Estos valores podrán variar en función de la tecnología y condiciones de operación.
H2, CO2 y metanol crudo: Estrategia de almacenamiento
En una planta de metanol típica, el límite inferior de operación suele estar en el rango de 30% a 50% de su capacidad máxima. Esto significa que la planta puede reducir su producción a un 30-50% de la capacidad nominal sin que se afecte significativamente el rendimiento, la calidad del metanol o la eficiencia energética.
Sin embargo, el límite exacto puede variar dependiendo del diseño específico de la planta, el tipo de tecnología utilizada, el control de la reacción catalítica, y las condiciones de operación. En algunos casos, optimizaciones tecnológicas pueden permitir un porcentaje más bajo.
Para garantizar el correcto funcionamiento de la planta, es fundamental realizar consideraciones específicas sobre el almacenamiento de materias primas, productos intermedios y finales. Estos aspectos no solo impactan la logística interna y externa, sino también la eficiencia operativa y la seguridad del proceso. A continuación, se detallan los principales factores a tener en cuenta en el diseño y gestión del almacenamiento.
Almacenamiento de Hidrógeno:
La electrólisis del agua para producir hidrógeno verde es una de las principales fuentes de consumo eléctrico en las plantas de metanol. La electricidad renovable, como la eólica o solar, es necesaria para garantizar que el hidrógeno se completamente renovable. Sin embargo, el acoplamiento a fuentes de energía renovable introduce una cierta variabilidad en la producción, lo que a su vez afecta la continuidad del suministro de hidrógeno.
Para asegurar un suministro constante y una operación fluida en la planta de metanol, es crucial un almacenamiento de hidrógeno adecuado. Este almacenamiento actuaría como un amortiguador, garantizando que la planta de metanol reciba un flujo continuo de hidrógeno, incluso cuando la producción esté sujeta a fluctuaciones de la energía renovable.
La capacidad y diseño de este sistema de almacenamiento dependerán de varios factores: el perfil de energía renovable, la distancia entre las instalaciones de producción de hidrógeno y la planta de metanol, el porcentaje del suministro de hidrógeno que provenga de producción in-situ o de proveedores externos. Todos estos elementos deben integrarse en la planificación para asegurar la estabilidad operativa y eficiencia de la planta de metanol. De forma general, debido al coste de almacenar hidrogeno, se recomienda una estrategia que garantice el suministro durante 10-20 horas.
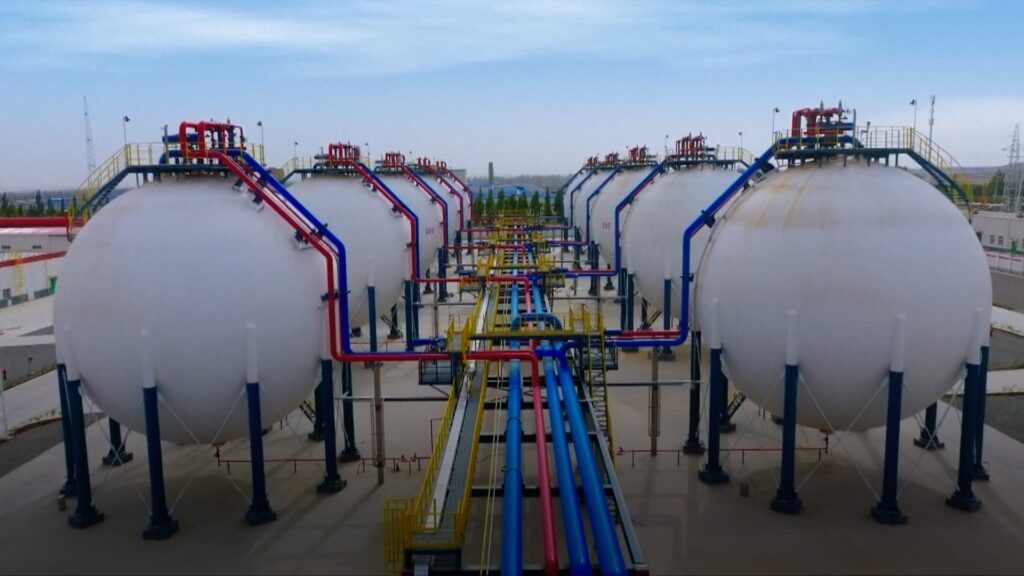
Ilustración 3 Almacenamiento de hidrógeno en planta china de 260 MW
Almacenamiento de CO2:
Aunque el perfil de producción de CO₂ es generalmente menos variable en comparación con el hidrógeno, también es fundamental contar con sistemas de almacenamiento adecuados. Esto garantiza la disponibilidad de CO₂ cuando la demanda lo requiera, permitiendo una mayor flexibilidad operativa ante fluctuaciones en suministro de CO2.
El CO₂ puede ser capturado in-situ o transportado a la planta de metanol mediante camiones, lo que implica que normalmente llegará en estado comprimido y líquido, o a través de conducciones de larga distancia, donde podría llegar en forma gaseosa a baja presión. Adicionalmente, el perfil de operación de la planta de captura y la planta de metanol, así como el porcentaje de producción es in-situ y suministro de terceros, son factores que deben tenerse en cuenta en la estrategia de almacenamiento.
Por lo tanto, la decisión entre almacenamiento en estado líquido o en esferas a baja presión dependerá de un análisis de todos estos factores, priorizando la eficiencia operativa, la seguridad y los costos. De forma general, dada la mayor facilidad de almacenamiento del CO2, con respecto al hidrogeno, se recomienda almacenar CO2 que garantice la alimentación de la planta entre 1-5 días.
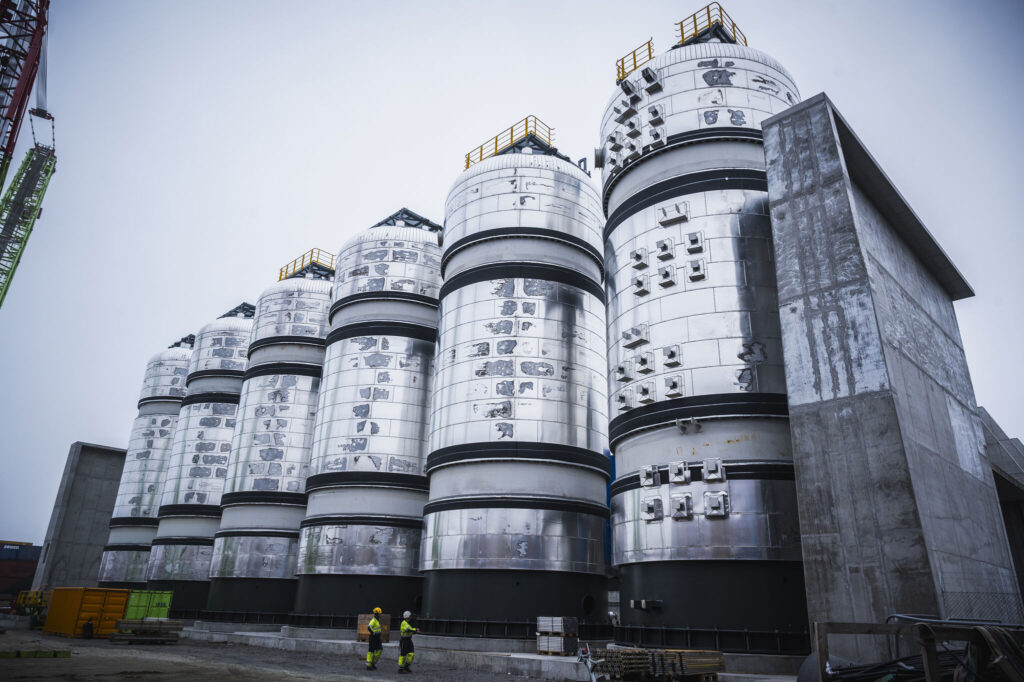
Ilustración 4 Almacenamiento de CO2 líquido en el proyecto Northern Lights
Almacenamiento de metanol crudo:
La destilación es un paso esencial para purificar el metanol. Sin embargo, los reactores de síntesis y las columnas de destilación tienen diferentes características en cuanto a flexibilidad operativa. El tanque de crudo intermedio permite que cada parte de la planta opere en sus condiciones óptimas. Si el reactor necesita operar a caudales más altos o más bajos debido a ajustes operativos, el tanque puede amortiguar esas variaciones, almacenando el exceso de crudo o suministrando material a la columna de destilación cuando sea necesario ya que la columna de destilación funciona de manera más eficiente cuando se alimenta a caudales constantes y estables. De este modo, se garantiza que la columna de destilación opere correctamente, optimizando su operación y reduciendo fluctuaciones en el proceso.
En cuanto al tiempo recomendado, este dependerá de los parámetros y perfiles de producción considerados en la planta, pero de forma general se recomienda que sea de al menos 1 día de producción de metanol crudo.
Te recomendamos escuchar el Episodio 69 de nuestro podcast: Metanol renovable con Diego Clemente (CETAER HUB) para complementar esta información de la mano de un profesional exitoso en el desarrollo de proyectos de metanol.
No olvides que desde AtlantHy trabajamos diariamente en proyectos de desarrollo de metanol con grandes éxitos en nuestra trayectoria. Tanto a nivel de consultoría e ingeniería como de tramitación de ayudas.
¡No dudes en contactarnos para hacer despegar tu proyecto de metanol renovable!
Si te ha gustado este artículo, permanece atento para seguir aprendiendo en la tercera parte, donde hablaremos sobre diversos aprendizajes en el planteamiento de este tipo de plantas… ¡Síguenos en AtlantHy Academy!
Referencias
IRENA. (2021). Renewable Methanol Outlook.
International Energy Agency. (2023). Carbon capture, utilisation and storage. Obtenido de https://www.iea.org/fuels-and-technologies/carbon-capture-utilisation-and-storage
Sollai, S. (2023). Renewable methanol production from green hydrogen and captured CO2: A techno-economic assessment. Journal of CO2 Utilization.