If you’ve already read the first article published on this forum about renewable ammonia, you’ll know that it’s a fundamental compound in our society—especially from a food production perspective. That’s why there’s such a strong emphasis on the need to decarbonise its production process, allowing the molecule to be used without generating greenhouse gas (GHG) emissions. However, as previously mentioned, this currently involves higher costs compared to the conventional fossil-based route, which can present challenges when it comes to adopting these renewable compounds—since consumers may not always be willing or able to accept a significant price increase, no matter how “green” the product may be.
In today’s publication, we’ll break down the key components of a renewable ammonia production plant, analysing:
- Raw material sourcing.
- Energy consumption.
- Expected capital expenditure for such a plant and the key parameters influencing ammonia production costs.
- Process optimisation strategies and how they can be integrated with RFNBO plants.
Raw material sourcing
The renewable ammonia production process begins with feedstocks consisting of hydrogen produced via water electrolysis and nitrogen obtained using renewable electricity, ensuring compliance with the RED III requirements for the production of RFNBOs (Renewable Fuels of Non-Biological Origin).
In terms of quantity, the process requires approximately 820 kg of nitrogen and 180 kg of hydrogen per tonne of ammonia. Since the reaction does not achieve complete conversion, the feedstocks must contain as few impurities and inerts as possible, as these would result in greater purge flows in the ammonia synthesis loop. The main impurities in this process are residual oxygenates in the feed streams (oxygen and water), which affect the performance of the iron-based catalysts used, as well as inerts such as argon.
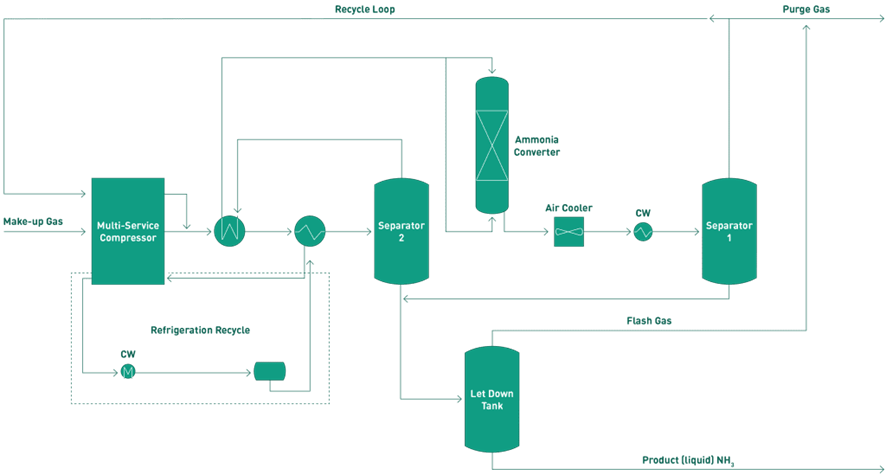
Illustration 1 Basic diagram of the renewable ammonia production process. Source: (Deepak Shetty, Rolf Postma and Nikolay Ketov, January 2024)
Hydrogen
As for hydrogen, since the electrolysis process generates a high-purity stream, the main contaminants are oxygen and water. These are easily removed through deoxygenation and drying stages using adsorbent beds, which are typically regenerated using thermal energy (TSA, Temperature Swing Adsorption). In this way, unlike conventional fossil-based hydrogen production methods, electrolysis offers greater simplicity in managing contaminants within an ammonia plant by producing a high-purity gas stream.
The following image shows the appearance of this type of purification system used for deoxygenation and drying of the hydrogen fed into renewable ammonia plants. In this case, the purification unit corresponds to the one installed at Yara’s plant in Herøya (Norway), where the hydrogen is supplied by a 24 MW PEM electrolysis system from ITM Power.
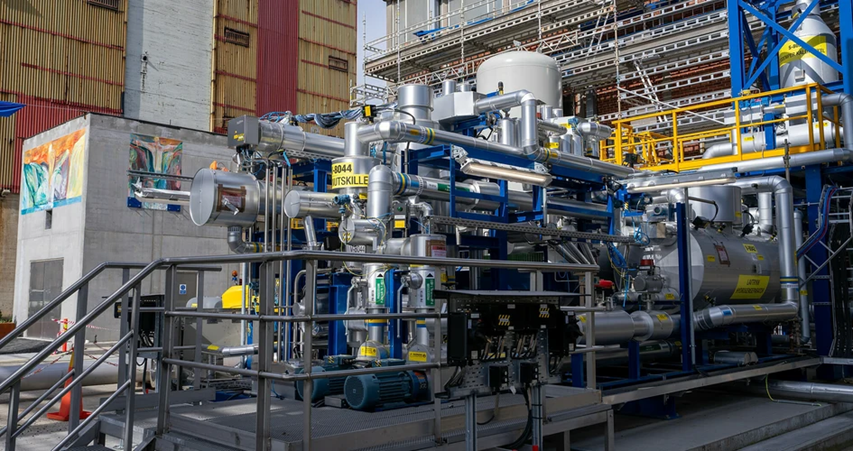
Illustration 2 Deoxygenation and hydrogen drying unit at Yara’s ammonia plant in Herøya (Norway). Source: (Yara, 2024)
Nitrogen
As for nitrogen, it can be supplied to the process in different ways depending on the scale of the plant. At the same time, regardless of the selected technology, the electricity used must come from renewable sources to ensure that the ammonia produced is sustainable.
At industrial scale, supplying nitrogen in gas cylinders would not be a viable option, as it would be impractical. While the purity would be ideal, the volumes provided through this method could not meet the required nitrogen demand in an economical and competitive way, since this solution is intended for very small consumers. Similarly, supplying liquid nitrogen would face the same limitations as gas cylinders—despite its extremely high purity, it would not be an attractive option from an economic standpoint.
For these reasons, the most attractive option is typically on-site nitrogen generation. The main alternatives for this are the use of membranes, pressure swing adsorption (PSA), or cryogenic air separation units (ASUs).
On the one hand, nitrogen generation using a membrane system can provide the volumes needed to meet the demand of an ammonia plant. However, this technology does not achieve very high nitrogen purity, with a significant presence of argon and oxygen impurities. As a result, these would need to be purged from the ammonia synthesis loop, leading to an energy penalty for the overall process and losses of raw materials—especially hydrogen.
Nitrogen production using a pressure swing adsorption (PSA) system can be suitable for achieving both the desired purity and flow rate. However, it does not allow for the generation of liquid nitrogen, which would be necessary for storage purposes to maintain a reserve supply of N₂ in case the PSA system fails—whether due to maintenance shutdowns or other deviations from the plant’s normal operating conditions.
The most suitable option, considering the limitations of membrane and PSA technologies, may be a cryogenic nitrogen generator. This type of system can supply a large volume of high-purity gaseous nitrogen to the ammonia synthesis process while simultaneously producing liquid nitrogen for later storage in a cryogenic tank. Before being fed into the synthesis loop, the stored liquid nitrogen must pass through vaporisation systems so that it can enter the process in its gaseous state.
Cryogenic nitrogen generators use the same cryogenic process as air separation units, but in this case, they are not designed to additionally produce high-purity oxygen and argon. Since their design focuses solely on producing pure nitrogen, both the capital investment and associated electricity consumption are reduced—resulting in a positive impact on the overall process economics.
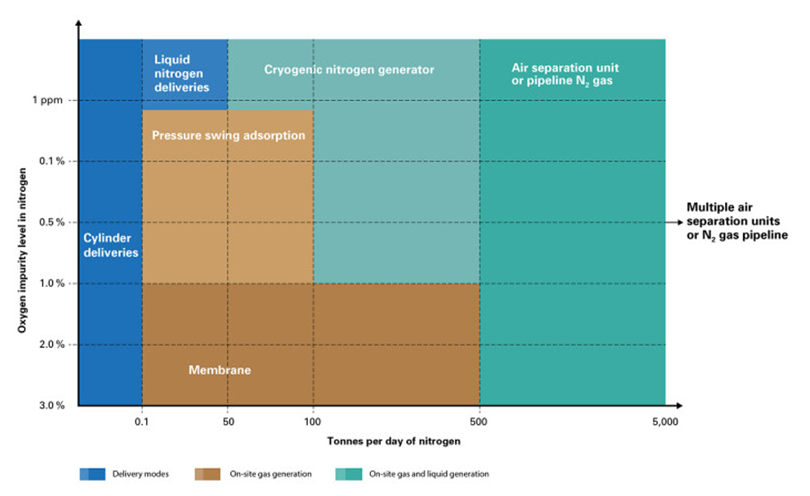
Illustration 3 Suitable nitrogen generation methods depending on required nitrogen capacity and purity (Pollution Solutions, 2024)
Energy consumption
Electricity consumption
Unlike in plants such as methanol production facilities, the ammonia production process relies exclusively on electrical energy, along with cooling systems (air- or water-based) to reduce the temperature of process streams, separate unreacted gases from the ammonia product, and achieve the desired final state of the ammonia—either liquefied by pressure at 16–18 bar at ambient temperature, or at atmospheric pressure and –33 °C.
In terms of scale, ammonia production consumes approximately 11 MWh per tonne of ammonia produced. This includes electrolysis, the Haber–Bosch process, gas compression, and nitrogen generation via ASU. Of this total consumption, assuming an electrolysis efficiency of 55 MWh per tonne of hydrogen produced, hydrogen generation accounts for around 90% of the plant’s electricity use. As a result, the OPEX is primarily driven by the cost of electricity used to produce hydrogen, and to a lesser extent by the power consumption of the synthesis loop compressors. This compression demand, in turn, depends heavily on the hydrogen feed pressure—meaning it is advantageous to obtain pressurised hydrogen directly from the electrolysis stage to reduce overall electricity consumption.
General consumption
As a reference, the typical consumption figures for a 100-tonne-per-day ammonia plant are as follows (assuming both plants operate the same number of hours per year):
Table 1. Typical consumption values for an ammonia plant with a capacity of 100 t NH₃/day.
Parameter | Value | Units |
Production capacity | 100 | t NH3/day |
Nitrogen consumption | 3.42 | t N2/day |
Hydrogen consumption | 0.76 | t H2/day |
Electrolysis power requirement | 42 | MWe |
Total plant power requirement | 46 | MWe |
Cooling demand | 0.5 | MWt |
Capital costs and cost of produced ammonia
Like nearly all industrial processes linked to hydrogen—such as methanol, SAF, and other derivative production—the Haber–Bosch process is highly dependent on economies of scale. This is illustrated in the following graph, which breaks down the impact of the different cost components depending on the plant size.
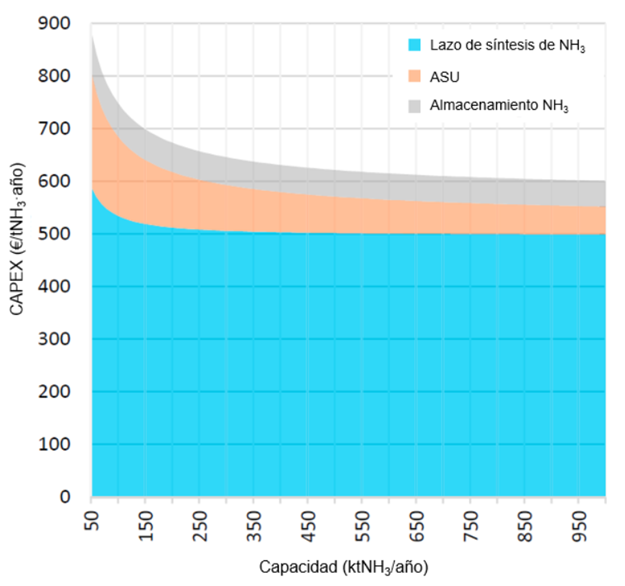
Chart 1. CAPEX of each subsystem by plant capacity (Fasihi, 2021)
The graph above shows how the specific capital cost of an ammonia plant decreases with increasing scale. However, it is important to note that in renewable ammonia projects, the main investment challenge is typically associated with hydrogen production. This is because, as an emerging market, the electrolysis systems currently available for dedicated hydrogen production are limited in size—generally up to 5 MW—and the manufacturing capacity for electrolysers remains relatively low. As a result, there is still significant room for cost reduction through increased production capacity and the automation of assembly and manufacturing processes.
For this reason, as scale increases, the capital cost of an ammonia plant will be heavily influenced by the cost of the associated electrolysis plant, since it does not offer the same cost reduction potential through increased production capacity.
Although economies of scale offer significant cost savings, in the short to medium term the trend is expected to shift towards small- or medium-scale plants. In such cases, the limiting factor is access to renewable electricity, which currently remains quite restricted in both capacity and availability—typically offering, at best, around 4,000 to 5,000 hours of renewable power supply per year.
In this context, when it comes to production costs, small- to medium-scale projects—ranging from 50 to 500 tonnes of ammonia per day—are heavily influenced by CAPEX. Due to the relatively limited production capacity, investment costs cannot be spread as efficiently over the plant’s lifetime as they can in larger-scale facilities.
One strategy to produce ammonia at a competitive cost is to minimise equipment size, which requires operating at very high pressures—typically above 300 bar. This pressurised operation helps reduce initial capital expenditure, and when combined with small- to medium-scale production (which also lowers OPEX due to lower overall energy consumption), it can help narrow the cost gap between renewable and conventional ammonia production. As a reference, a renewable ammonia plant with a capacity of 100 tonnes per day could require an investment of around €35–45 million.
For these reasons, although renewable ammonia currently has a much higher cost than its fossil-based counterpart, it is expected that over time—and with improvements in production processes, particularly in the cost and energy consumption of electrolysis—it will reach cost parity with conventional ammonia, as shown in the following illustration:
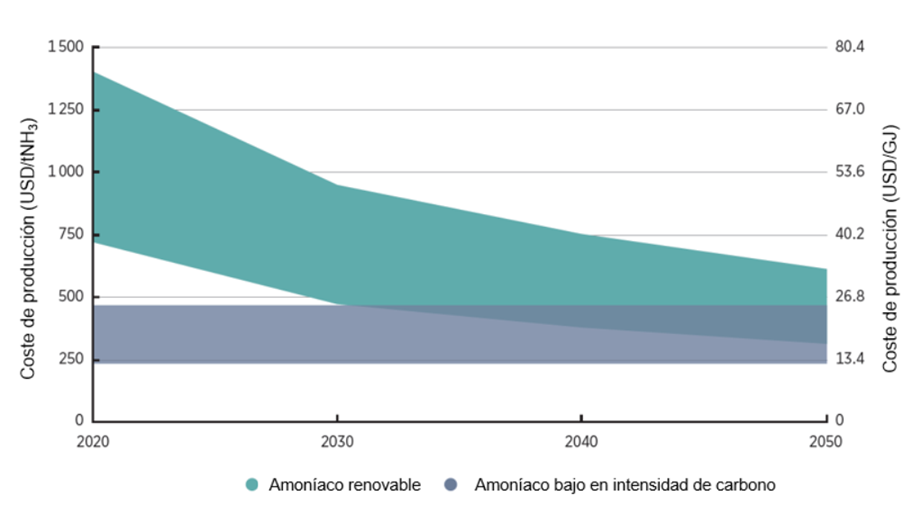
Chart 2. Ammonia production costs by 2050 in a decarbonised scenario (IRENA, 2022)
Integration into RFNBO plants
With regard to integration into RFNBO fuel plants, the main drawback of ammonia facilities—similar to methanol plants—is their rigidity, as they need to operate at no less than 40% of their design flow rate to ensure the process runs correctly and relatively efficiently.
For this reason, it is essential to ensure that, while a constant and continuous supply of renewable electricity throughout the year is not yet possible, there is sufficient flexibility in the hydrogen supply to meet the minimum load threshold of the ammonia synthesis loop. This is why intermediate hydrogen storage systems are often proposed—to cover those hours when renewable resources are unavailable, primarily at night when solar photovoltaic plants are not producing electricity.
These types of storage systems provide flexibility, but they also increase the plant’s capital cost, which economically penalises the final price of the ammonia produced. Therefore, when sizing the storage system, it is important to find a compromise between flexibility and added investment cost, in order to keep the overall capital increase within reasonable limits.
Regarding potential synergies with other renewable processes, it is worth highlighting that the ammonia synthesis reaction is exothermic—that is, it releases large amounts of heat. In some cases, technology providers choose not to recover this heat and instead dissipate it into the atmosphere, for example through an air-cooling system. However, one potential application of this heat could be to use it for steam generation, which could then be fed into a turbine system to produce electricity and reduce power consumption. Alternatively, the steam could be fed into a solid oxide electrolyser (SOEL).
In the latter case, the use of steam would allow electricity demand for hydrogen production to be reduced by approximately 30%, lowering the requirement from 55 MWh per tonne of hydrogen to around 39–40 MWh. This would have a positive impact on the plant’s OPEX and, consequently, on the cost of ammonia production. At the same time, the overall power requirement of the plant would be reduced, making it more feasible to secure available capacity at existing substations.
For this reason, and as mentioned in other posts on the development of both methanol plants and CO₂ capture facilities, it is crucial during the design and development phase of a project to analyse the synergies between the streams of all processes involved. Process integration can lead to significant improvements in energy consumption, helping to reduce operational costs and increase the economic competitiveness of renewable alternatives compared to fossil-based compounds.
If you want to learn more about renewable ammonia plants, listen to Episode 59 of our podcast with Mauricio Medici.
And don’t forget—at AtlantHy, we support renewable ammonia project development every day, offering consulting, engineering, and assistance with funding applications.
Don’t hesitate to contact us to get your renewable ammonia project off the ground!
If you enjoyed this article, stay tuned to keep learning about the planning and development of these kinds of projects.
Follow us on AtlantHy Academy!
References
Deepak Shetty, Rolf Postma and Nikolay Ketov. (January 2024). Green ammonia, right where you need it. Hydrogen Tech World.
Fasihi, M. (2021). Global potential of green ammonia based on hybrid PV-wind power plants. Applied Energy.
IRENA. (2022). Innovation Outlook Renewable Ammonia. Abu Dhabi.
Pollution Solutions. (Enero de 2024). Nitrogen as a utility gas and feedstock for green ammonia. Retrieved from https://www.pollutionsolutions-online.com/news/green-energy/42/sbh4-gmbh/nitrogen-as-a-utility-gas-and-feedstock-for-green-ammonia/61677
Yara. (2024). Yara opens renewable hydrogen plant: “A major milestone”. Retrieved from https://www.yara.com/corporate-releases/yara-opens-renewable-hydrogen-plant-a-major-milestone/