Would you buy a car without test-driving it first or making sure it won’t break down the moment you leave the dealership? Probably not. The same applies to electrolyzers. In a field as strategic as renewable hydrogen production, blindly trusting a piece of equipment without thorough validation can be extremely costly. A well-executed FAT (Factory Acceptance Test) is your guarantee that the system about to leave the factory won’t let you down when you need it most.
Today, with the hydrogen sector just getting underway, a FAT is not just recommended — it’s essential. Here we explain what a proper FAT should look like, what it includes, why it’s critical before receiving an electrolyzer, and which mistakes you need to avoid.
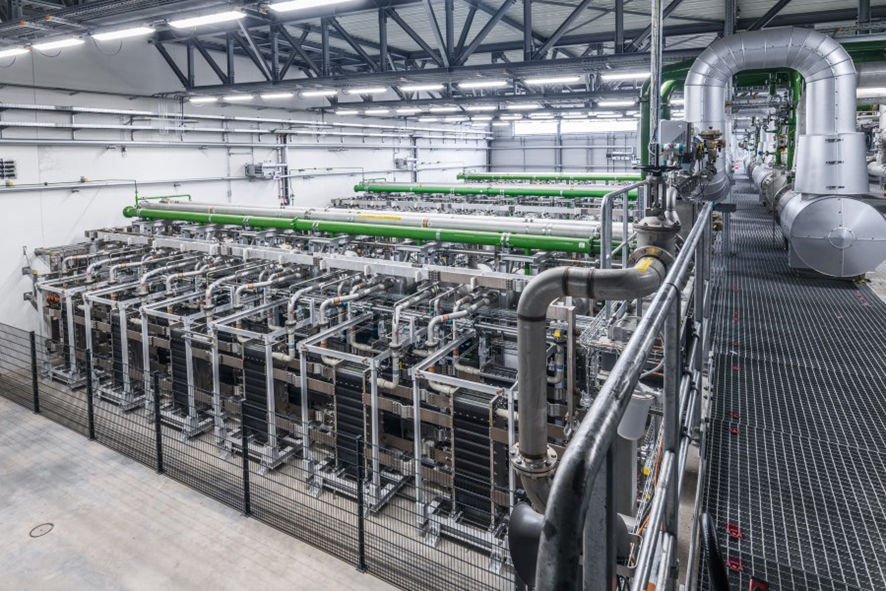
Illustration 1. 54 MW electrolysis system installed at BASF’s Ludwigshafen plant (Hydrogen Tech World, 2025).
What is a FAT and why is it so important in an electrolyzer?
A FAT is the final major test before an electrolysis system leaves the factory. It’s not just about switching it on and checking for error messages: a FAT is a comprehensive validation of performance, safety, operational flexibility, hydrogen purity, and overall reliability. It is carried out under controlled conditions, recording critical parameters, and ideally in the presence of client representatives.
The FAT enables early detection of faults before the equipment is shipped to its final location, helping avoid costly downtime, remote interventions, or delays in projects with tight commissioning windows.
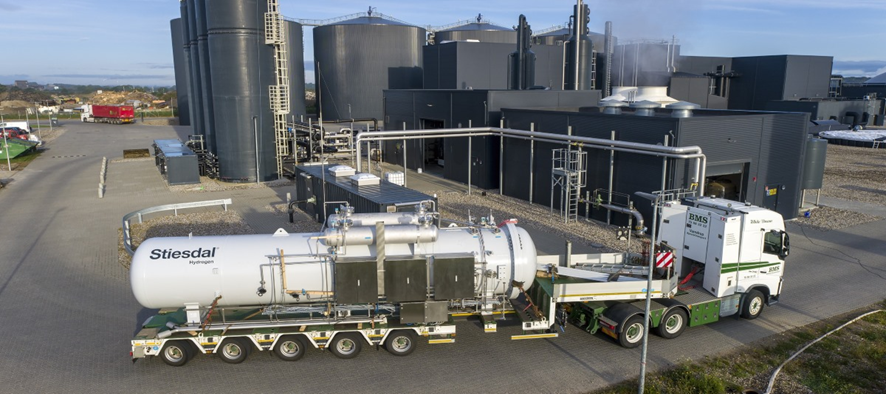
Illustration 2. Transport of an electrolyser by Stiesdal (Hydrogen Tech World, 2024).
What should a FAT for electrolysers include?
A well-designed FAT goes far beyond simply switching on the equipment and checking that it runs—it must assess all the system’s critical aspects, from actual production capacity to hydrogen quality and performance under load changes. All of this is done through structured tests that examine the main functional blocks of the electrolyser:
- Production and energy efficiency: Does it produce the expected output at the agreed consumption rate?
- Leak tightness and pressure resistance: Is the system safe and free of leaks?
- Operational flexibility under variable loads: Can it respond adequately to the fluctuations expected from the power supply?
- Quality of the hydrogen produced: Does it meet the required purity level for its intended end use?
- Control and safety systems: Do they operate correctly?
Production and energy consumption verification
The amount of hydrogen produced at different load levels is measured to ensure it remains within the design range. Additionally, the energy efficiency (kWh/kg of H₂) is analysed under initial operating conditions (Beginning of Life, BOL).
Pressure and leak tightness test
The system is pressurised to the nominal pressure level or slightly above, and any pressure drop is recorded over a controlled period. This test ensures the integrity of stacks, valves, sensors, and mechanical joints, as it allows leaks to be detected if a significant pressure drop is observed.
This step guarantees the mechanical integrity of the equipment, since even a microleak can cause operational issues or compromise safety in the field, especially considering that these systems handle hydrogen and oxygen.
Load ramps: simulating operational reality
Electrolysers must be capable of responding flexibly to variable renewable generation profiles. For this reason, a well-designed FAT includes:
- Upward ramps from minimum loads (10–30%) to 100%, with defined and controlled steps.
- Progressive decreases down to the technical minimum (~10%), monitoring stability and efficiency.
- Sustained full-load cycles for at least one hour to validate the reliability of the measured results.
- Dynamic events, such as abrupt load changes (e.g. from 40% to 90%), simulating real operating conditions.
These tests make it possible to identify potential issues with power regulation, thermal response, production stability and gas quality, as well as to ensure equipment safety across the full operating range, since partial loads can lead to gas crossover problems.
Hydrogen quality: does it meet the purity required for its final use?
One of the most important validations during the FAT is to ensure that the hydrogen produced meets the minimum purity required for its final application, whether for use as fuel or for the production of derivatives such as ammonia, SAF or methanol. During the FAT, the following parameters are monitored online:
- Oxygen content (O₂).
- Humidity or water vapour (H₂O).
- Presence of trace contaminants, such as KOH in alkaline electrolysers.
Depending on the offtake, the required purity levels can vary:
- In processes where hydrogen is used as fuel in furnaces, a slightly higher level of impurities may be acceptable; however, for mobility applications, a higher purity is required (99.999% H₂).
- For chemical synthesis, ultrapure hydrogen is necessary (O₂ < 1 ppm, H₂O < 10 ppm, typically).
Inadequate purity can compromise integration with the derivative production process or even damage downstream equipment from the electrolysis system.
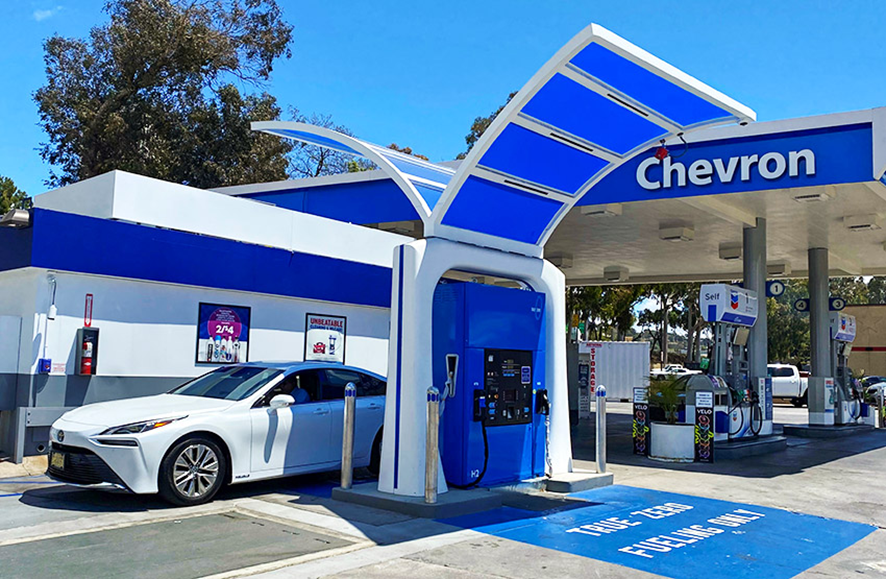
Illustration 3. Hydrogen dispensing station for vehicles (Hydrogen Fuel Cell Partnership, 2021).
Safety and control systems
During the FAT, nearly all critical elements of the control system are tested:
- Pressure, temperature, humidity, and H₂ presence sensors in O₂ lines.
- Safety interlocks and emergency shutdown logics.
- Visual alarms and event logs.
- Response time to critical events.
All of this must be displayed through a Human Machine Interface (HMI), allowing real-time access to data such as efficiency, electrical consumption, valve statuses, alarm signals, and more.
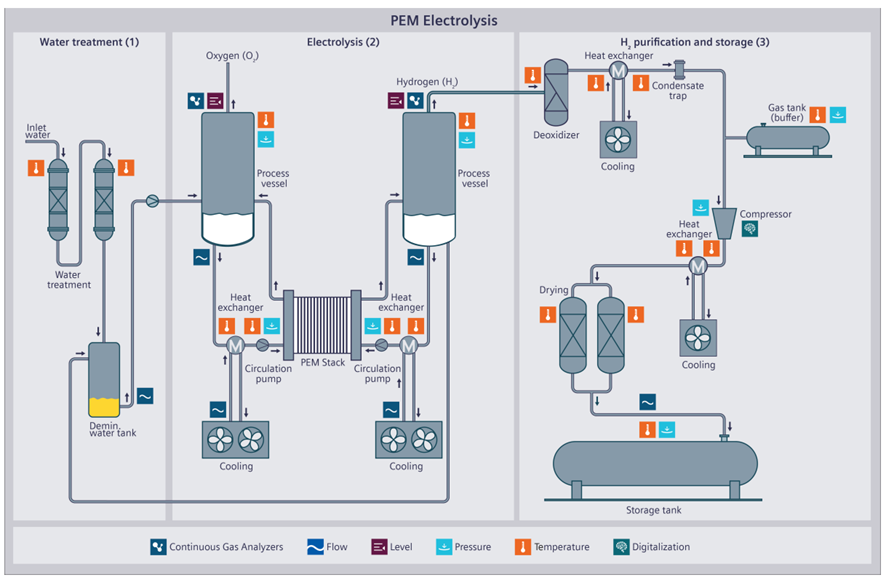
Illustration 4. SIEMENS HMI for a PEM electrolysis system (Siemens, 2023).
How should a FAT be observed?
Whenever possible, it is ideal for the client or end user to be present during the FAT to directly observe the electrolyser’s behaviour—from start-up to hydrogen production.
If this is not feasible, the entire operation can be monitored from a control room, where an HMI displays each relevant parameter and allows decisions to be made or results validated without physically accessing the installation.
Traceability and documentation: FAT essentials
A high-quality FAT must produce a complete and traceable record of everything that has been verified:
- Pressure, flow, load ramp and purity graphs.
- Step-by-step validated checklists.
- Alarms and events logged with time stamps.
- KPIs tabulated by load point and efficiency.
- Documentation for all tested equipment, certified as compliant with applicable regulations.
This level of documentation not only validates the FAT itself, but also ensures traceability of results and purchased equipment.
Conclusions
The FAT is the first major audit of an electrolyser. Executing it rigorously means:
- Validating that the system produces hydrogen safely and efficiently.
- Avoiding failures in the field that could delay projects.
- Reducing financial risk for investors and clients.
In a context where hydrogen demand is expected to multiply fivefold by 2050, each unit must perform and produce renewable hydrogen safely and efficiently from the very first kilowatt fed into the system.
A well-executed FAT ensures the equipment delivers—so it’s not just another formality: it’s the gatekeeper that separates a reliable installation from a problem that will eventually show up during operation.
If you’re preparing a renewable hydrogen project and need technical support, don’t hesitate to contact us!
Follow us at AtlantHy Academy!
References
Hydrogen Fuel Cell Partnership. (2021). Studio City Hydrogen Station Opens. Retrieved from https://h2fcp.org/blog/studio-city-hydrogen-station-opens
Hydrogen Tech World. (2024). Stiesdal Hydrogen: industrializing green hydrogen production. Retrieved from https://hydrogentechworld.com/stiesdal-hydrogen-industrializing-green-hydrogen-production
Hydrogen Tech World. (2025). BASF commissions 54-MW electrolyzer to decarbonize hydrogen production at its Ludwigshafen site. Retrieved from https://hydrogentechworld.com/basf-commissions-54-mw-electrolyzer-to-decarbonize-hydrogen-production-at-its-ludwigshafen-site
Siemens. (2023). Green Hydrogen Process Analytics and Instrumentation Solution. Retrieved from https://assets.new.siemens.com/siemens/assets/api/uuid:0836abe5-5216-4cb7-af31-29cd5f4f2f16/dipa-b10287-00-7600flyergreen-hydrogen-300.pdf
Hydrogen Tech World. HTW Editorial Team. (29/02/2024). Green Hydrogen Systems’ X-Series electrolyser prototype achieves key milestone. Retrieved from https://hydrogentechworld.com/green-hydrogen-systems-x-series-electrolyser-prototype-achieves-key-milestone (Cover image)