As we saw in the previous article, methanol is emerging as a key component in the transition to a more sustainable future across various sectors, including transportation and, most notably, the maritime industry. With the increase in regulatory demands and the need to reduce CO₂ emissions, e-methanol is positioned as a viable alternative to traditional fuels. This synthetic fuel, considered a type of RFNBO (Renewable Fuels of Non-Biological Origin), is produced using H₂ generated from renewable electricity, along with resources such as water and captured carbon dioxide (CO₂).
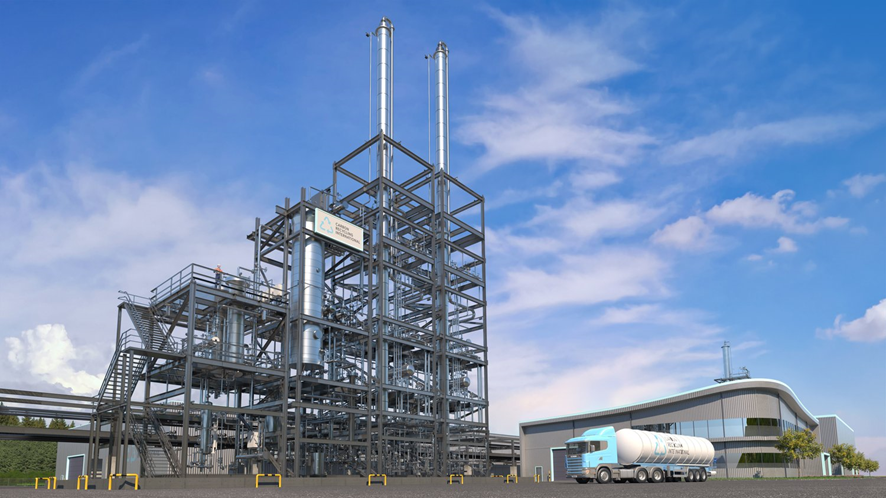
Illustration 1: Methanol plant located in Iceland (capacity 4,000 tons per year).
Investment Costs
The main barrier to the adoption of renewable methanol is the same as for other alternative fuels and renewable feedstocks: the production cost. Developing e-methanol production plants involves significant investment. For example, a plant capable of producing 60,000 tons per year may require an estimated investment of €70–90 million, not including the hydrogen production plant.
In the e-methanol production process, compressed hydrogen and carbon dioxide are introduced into the methanol reactor, where CO₂ hydrogenation takes place in the presence of a copper, zinc, and aluminum catalyst. The reaction occurs at high pressures (40–100 bar) and temperatures (200–300 °C), producing crude methanol, which contains methanol and water. Since the reaction is exothermic, the heat generated is dissipated using water as coolant (which evaporates), or by cooling the gas mixture. Once the crude methanol is obtained, it is sent to a distillation system where methanol and water are separated to obtain nearly pure streams of both. The residual heat from the reactor can be used in this stage to reduce the external energy required for distillation, optimizing energy efficiency (IRENA, Renewable Methanol Outlook, 2021; Sollai, 2023).
Thus, a methanol production plant from CO₂ and hydrogen resembles a conventional chemical plant in terms of infrastructure, processes, and equipment used, such as reactors, compressors, and control systems. As in traditional petrochemical production, methanol synthesis involves catalytic reactions at high pressure and temperature, enabling the application of economies of scale. This means that as plant production capacity increases, unit operational and capital costs decrease significantly, making green methanol production more competitive and viable on a large scale.
E-Methanol Consumption
The e-methanol production process requires a combination of green hydrogen and captured carbon dioxide. In terms of inputs, 0.2 tons of hydrogen (H₂) and 1.4 tons of CO₂ are required to produce 1 ton of methanol.
Regarding utilities consumption, the production of e-methanol requires 0.8 MWh of electricity, 0.23 MWh of thermal energy per ton of methanol, and 2 MW of heat dissipation per ton. For example, the following table shows a base case with estimated raw material needs and utility consumption for a plant with a 60,000-ton-per-year capacity:
Table 1: Estimated Consumption for a 60 KTA Methanol Plant
Parameter | Value |
Annual H₂ Consumption (t) | 12.000 |
CO₂ Consumption (t) | 84.000 |
Electricity Consumption (MW) | 6 |
Thermal Demand (MWt) | 1,7 |
Cooling Demand (MWt) | 15 |
These consumption values are estimates and may vary depending on operating conditions and the pressure at which hydrogen (H₂) and carbon dioxide (CO₂) are received. In this reference case, it is assumed that both CO₂ and H₂ arrive at atmospheric pressure, resulting in high energy consumption due to the need to compress both streams. Energy consumption could be significantly reduced if the feedstocks were supplied at pressures closer to operating conditions.
Cost-Limiting Factors
The main barrier to the adoption of renewable methanol is again the production cost (IRENA, Renewable Methanol Outlook, 2021).
In the case of e-methanol, it’s important to highlight the crucial role played by the production cost of CO₂ and H₂ in determining the final cost of methanol. For example, assuming €4,000/ton for hydrogen and €100/ton for CO₂, the base cost of methanol would be €940/ton. This base cost reflects only the raw material cost, which accounts for about 80% of the final methanol cost.
In the following image, the variation of the estimated methanol price can be observed as a function of the cost of hydrogen and CO₂. This relationship is crucial to understanding the competitiveness of e-methanol production.
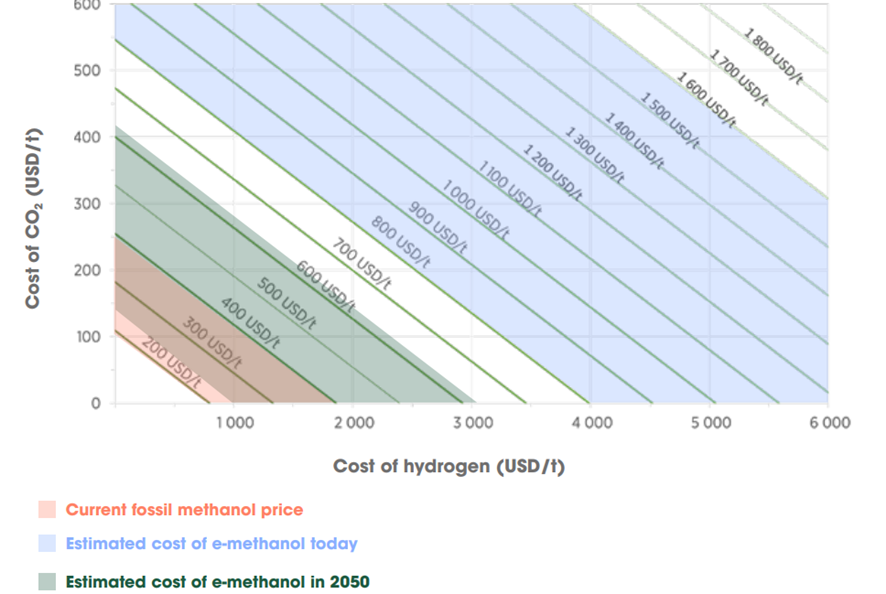
Illustration 2: Methanol cost as a function of H₂ and CO₂ prices (IRENA, Renewable Methanol Outlook, 2021).
Thus, the main barrier to the production of e-methanol from CO₂ and hydrogen is its high cost, especially due to the electrolysis of water to produce hydrogen, which consumes around 55 MWh per ton of H₂. Therefore, reducing the price of renewable energy is key to lowering the current cost of e-methanol to more competitive levels.
Methanol Plant Integration Strategies
CO₂ Purity and the Catalyst: Importance and Effects
One of the key aspects in renewable methanol production is the purity of CO₂. For an efficient conversion into methanol, CO₂ must minimize its contaminants and impurities, as they could deactivate the catalysts and reduce the process efficiency.
– Catalysts and their sensitivity: Typical catalysts used in methanol production include copper, zinc, and aluminum, and they are sensitive to impurities that interfere with their activity. The presence of contaminants can poison the catalysts, decreasing the CO₂ conversion rate and affecting the overall productivity of the plant.
– Impact of inerts: Inert gases such as nitrogen or argon do not participate in methanol formation reactions. Their presence reduces the concentration of reactants (H₂ and CO₂) in the reaction mixture, which dilutes the process, potentially causing less interaction with the active sites of the catalyst, and increases energy consumption due to the need to compress or recycle larger gas volumes. Thus, they reduce the plant’s overall energy efficiency.
For the methanol production plant, a CO₂ purity of 99.6% is expected, while an H₂ purity of 99.8% is required. These values may vary depending on the technology and operating conditions.
H₂, CO₂, and Crude Methanol: Storage Strategy
In a typical methanol plant, the lower operational limit is usually between 30% to 50% of its maximum capacity. This means the plant can reduce production to 30–50% of its nominal capacity without significantly affecting performance, methanol quality, or energy efficiency.
However, the exact limit may vary depending on the plant’s specific design, the type of technology used, the control of the catalytic reaction, and the operating conditions. In some cases, technological optimizations may allow for a lower percentage.
To ensure proper plant operation, specific considerations must be made regarding the storage of raw materials, intermediate products, and final outputs. These aspects impact not only internal and external logistics but also operational efficiency and process safety. The main factors to consider in the design and management of storage are detailed below.
Hydrogen Storage:
Water electrolysis to produce green hydrogen is one of the main sources of electricity consumption in methanol plants. Renewable electricity, such as wind or solar, is required to ensure that the hydrogen is fully renewable. However, coupling with renewable energy sources introduces some variability in production, which in turn affects the continuity of hydrogen supply.
To ensure a constant supply and smooth operation of the methanol plant, proper hydrogen storage is crucial. This storage acts as a buffer, ensuring the methanol plant receives a continuous hydrogen flow even when production is subject to fluctuations in renewable energy.
The capacity and design of this storage system will depend on several factors: the renewable energy profile, the distance between the hydrogen production facilities and the methanol plant, and the percentage of hydrogen supply coming from on-site production or external providers. All these elements must be integrated into the planning to ensure operational stability and efficiency of the methanol plant. In general, due to the cost of hydrogen storage, a strategy that ensures supply for 10–20 hours is recommended.
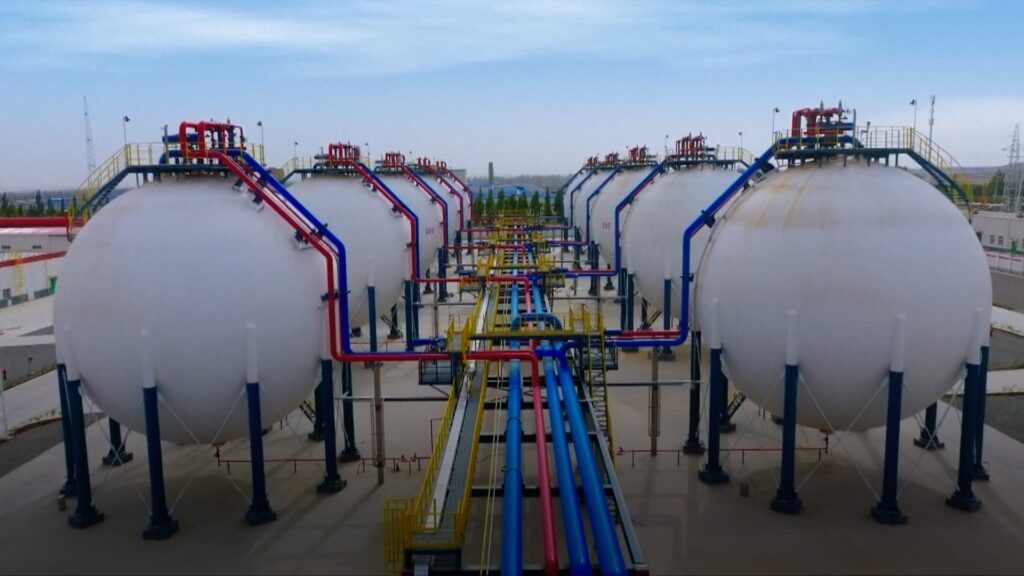
Illustration 3: Hydrogen Storage at a 260 MW Plant in China
CO₂ Storage:
Although the CO₂ production profile is generally less variable compared to hydrogen, it is also essential to have proper storage systems. This ensures CO₂ availability when demand requires it, allowing for greater operational flexibility in the face of CO₂ supply fluctuations.
CO₂ can be captured on-site or transported to the methanol plant by trucks, which typically means it will arrive in a compressed and liquid state, or through long-distance pipelines, where it may arrive in a gaseous form at low pressure. Additionally, the operating profile of the capture plant and the methanol plant, as well as the percentage of on-site production versus third-party supply, are factors that must be considered in the storage strategy.
Therefore, the decision between liquid storage or low-pressure sphere storage will depend on an analysis of all these factors, prioritizing operational efficiency, safety, and cost. In general, given the greater ease of storing CO₂ compared to hydrogen, it is recommended to store enough CO₂ to ensure plant feed for 1–5 days.
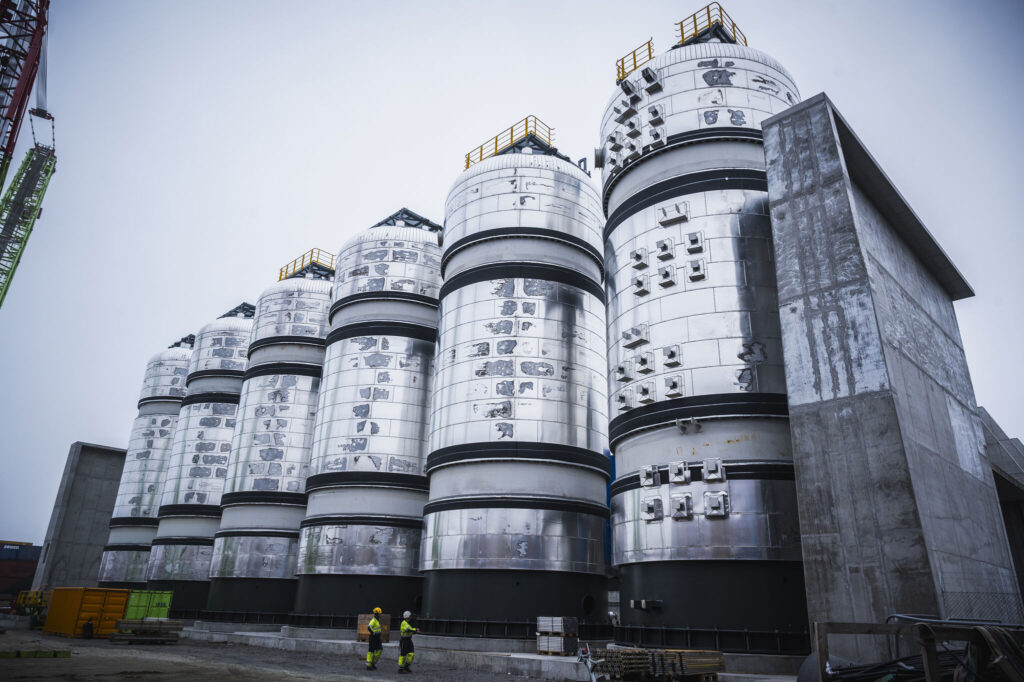
Illustration 4: Liquid CO₂ Storage in the Northern Lights Project
Crude Methanol Storage:
Distillation is an essential step to purify methanol. However, synthesis reactors and distillation columns have different characteristics in terms of operational flexibility. The intermediate crude tank allows each part of the plant to operate under optimal conditions. If the reactor needs to operate at higher or lower flow rates due to operational adjustments, the tank can buffer those variations, storing excess crude or supplying material to the distillation column when needed, since the distillation column operates more efficiently when fed at constant and stable flow rates. This ensures that the distillation column works properly, optimizing its performance and reducing fluctuations in the process.
As for the recommended storage time, this will depend on the parameters and production profiles considered in the plant, but in general it is recommended to store the equivalent of at least one day of crude methanol production.
We recommend listening to Episode 69 of our podcast: Renewable Methanol with Diego Clemente (CETAER HUB) to complement this information from the perspective of a successful professional in methanol project development.
Don’t forget that at AtlantHy, we work daily on methanol development projects with great success in our track record both in consulting and engineering, as well as in securing public funding.
Feel free to contact us to help launch your renewable methanol project!
If you enjoyed this article, stay tuned for the third part, where we will discuss key learnings in the design of these types of plants… Follow us on AtlantHy Academy!
References
IRENA. (2021). Renewable Methanol Outlook.
International Energy Agency. (2023). Carbon capture, utilisation and storage. Obtenido de https://www.iea.org/fuels-and-technologies/carbon-capture-utilisation-and-storage
Sollai, S. (2023). Renewable methanol production from green hydrogen and captured CO2: A techno-economic assessment. Journal of CO2 Utilization.