Methanol is undoubtedly hydrogen’s great ally in enabling its penetration into the maritime and chemical sectors. This molecule, with a current consumption of over 100 million tons per year, offers an immediate use for hydrogen in renewable hydrogen projects, which explains why a large part of promoters are seeking to orient their current projects toward the production of renewable methanol.
In this AtlantHy Academy article, we share the lessons we’ve learned from developing several methanol plants in recent years.
Introduction to Methanol
Methanol (CH₃OH) is a colorless liquid soluble in water with a slight alcoholic odor. It freezes at -97.6°C, evaporates at 64.6°C, and has a density of 791 kg/m³ at 15°C (IRENA, Renewable Methanol Outlook, 2021).
Currently, methanol is one of the four most produced chemical compounds globally, along with other critical compounds such as ethylene, propylene, and ammonia. The annual demand for this compound nearly doubled over the last decade, reaching approximately 110 Mt in 2023 (BloombergNEF), while global production capacity has reached around 183 Mt, with 70% centered in China.
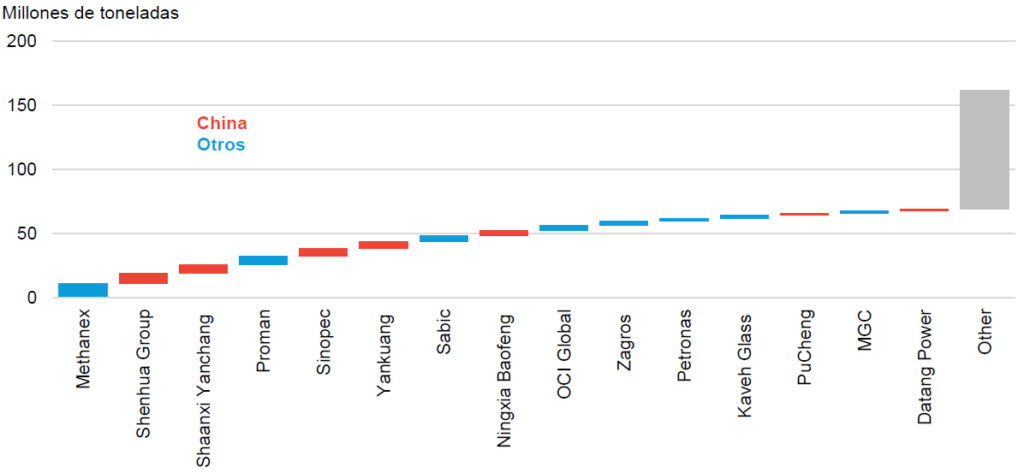
Currently, 2/3 of its production capacity is destined for the synthesis of chemical compounds such as formaldehyde, acetic acid, methyl methacrylate, and ethylene and propylene through the methanol-to-olefins (MTO) route. These chemical compounds are subsequently processed to produce hundreds of essential daily life products, from paints and plastics to automotive components and construction materials (IRENA & Methanol Institute, 2021). At the same time, its use for the production of aromatic compounds such as xylene, benzene, and toluene is also being considered, although this route (Methanol-to-Aromatics, MTA) is still under development (IEA, The Future of Hydrogen, 2019).
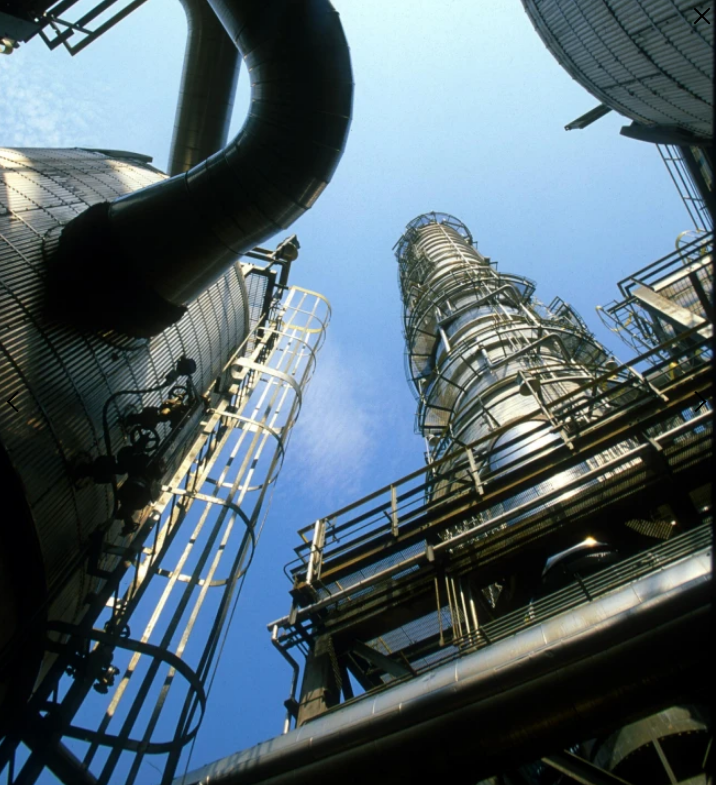
The second major use of methanol is as a fuel, used either alone or mixed with other fuels. Demand in this sector has also grown rapidly in recent years, with the direct use of methanol as a fuel increasing by over 14% in 2021. The following graph shows the growth in methanol demand in recent years, reaching an annual growth rate of 3.5% (IRENA, 2021).
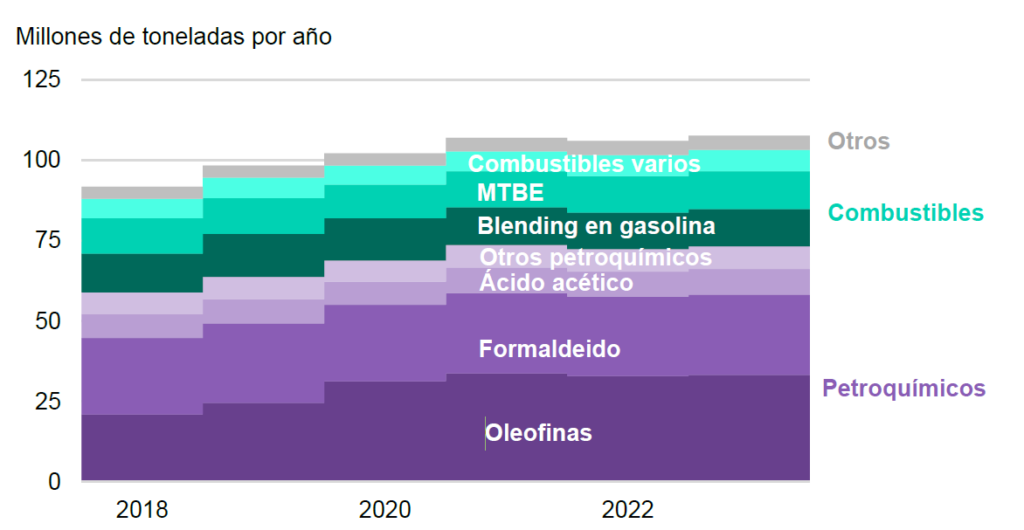
As today’s global MEOH production is based on the use of natural gas or coal, emissions from current methanol production and use are around 0.3 gigatons (Gt) of CO2 per year (around 10% of total chemical sector emissions), highlighting the need to decarbonize these activities.
However, methanol can also be produced from other carbon-containing feedstocks, including biomass, biogas, waste streams, and captured CO2 from numerous sources. Renewable methanol can be produced using renewable energy and renewable feedstocks through two routes:
- Biological Route: In this case, it is known as biomethanol and is produced from biomass. The main sustainable biomass feedstocks include: forest and agricultural waste and byproducts, landfill biogas, wastewater, MSW, and black liquor from the pulp and paper industry.
- Power-to-X Route: Methanol obtained via this route is known as e-methanol, and the process requires renewable hydrogen, i.e., hydrogen produced from renewable electricity via electrolysis, and captured carbon dioxide.
In the current context of the energy transition, the production of synthetic methanol obtained from CO2 and renewable hydrogen presents itself as an alternative that several countries have embraced; the Methanol Institute estimates that there are currently more than 174 renewable methanol projects worldwide and that by 2030, more than 11 Mt of this compound will be produced.
Although various renewable methanol production technologies currently exist, some are still in development stages, with the one showing the most potential being that which produces the necessary hydrogen through water electrolysis (Illustration 1). This hydrogen must then be combined with carbon dioxide in a reactor to form methanol. The e-methanol synthesis stage is very similar to the methanol production from synthesis gas based on fossil fuels and therefore, this technology has a high level of maturity (TRL 8–9).
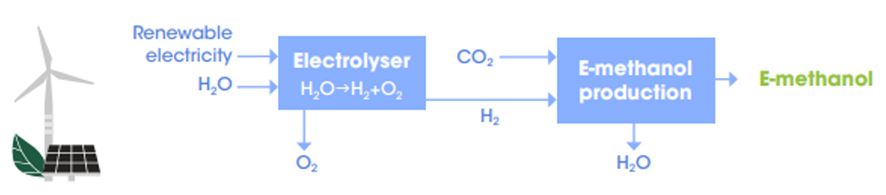
Therefore, it is necessary to emphasize that synthetic renewable methanol production, that is, one in which hydrogen is produced from water electrolysis, consists of the combination of hydrogen with carbon dioxide in a catalytic reactor to enable the hydrogenation of CO2.
Renewable Methanol Production Process
Each mol of CO2 will be converted into one mol of methanol, requiring three hydrogen molecules and producing one mol of water as a byproduct. The methanol synthesis process from CO2 hydrogenation can be described by three equilibrium reactions, which are the hydrogenation of CO2 (1), the reverse water-gas shift reaction (2), and the hydrogenation of CO (3) (Sollai, 2023) (Nieminen, 2019):

Thermodynamically, the hydrogenation of CO2 to CH3OH is favorable for CH3OH production at low temperatures and high pressures due to the exothermic reaction and the lower number of product moles. Besides CH3OH production, this reaction is often accompanied by carbon monoxide (CO) production in a step also known as the reverse water-gas shift reaction (RWGS) (Yang, 2022):

As for the reaction temperature, the RWGS reaction is endothermic, and more CO will be produced at high temperatures. Overall, the reaction temperature must be relatively low to achieve excellent selectivity toward CH3OH. However, at low temperatures, the CO3 conversion rate is very low. Therefore, it is a challenge for CO2 hydrogenation to CH3OH to achieve high conversion and selectivity simultaneously. The CO produced reacts with hydrogen, similarly to conventional reactors, to produce methanol following this reaction:

The most efficient catalysts for CO2 hydrogenation to methanol are multi-component catalytic systems. As for the conditions of this process, they are virtually identical to the conventional process, since the reaction occurs at temperatures between 200°C and 300°C and pressures of 40–100 bar (IRENA, Renewable Methanol Outlook, 2021).
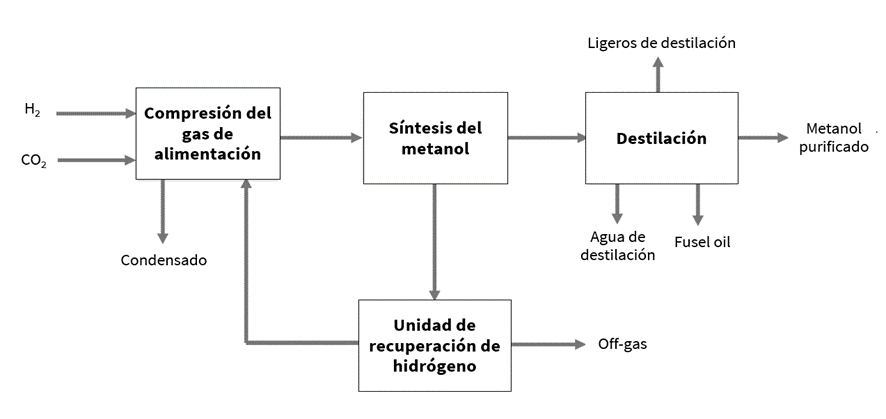
As seen in the general e-methanol production process diagram, the hydrogen and carbon dioxide feedstocks are compressed to the necessary pressure value in the synthesis stage and are introduced into the methanol production reactor.
The reactor is the unit in which methanol is produced via carbon dioxide hydrogenation. In this equipment, at high pressure (40–100 bar) and high temperature (200–300 °C), the hydrogenation reaction of CO2 occurs through the combination of hydrogen and carbon dioxide in the presence of a catalyst based on copper, aluminum, and zinc (Cu/ZnO/Al2O3), yielding a stream of methanol and water (byproduct) known as crude methanol[1].
Since the CO2 hydrogenation process is exothermic (releases energy), a heat removal system is required, which may involve either using water as a coolant which evaporates and forms steam using the residual heat of the reaction (Boiling Water Reactor/BWR) or cooling with the reactor’s incoming gas (a mixture of H₂ and CO2), so that the reactor’s outlet stream is used to preheat the hydrogen and carbon dioxide mixture fed into the synthesis loop.
Once methanol has formed in the reactor, it is directed to the distillation system, as this compound exits diluted in water. In this system, CH3OH and H2O, as well as other possible byproducts, are separated, obtaining nearly pure streams of both compounds. To do this, energy in the form of heat must be applied, so the residual heat produced in the reactor as a result of the reactions could be integrated with this column’s thermal requirements, reducing the need for additional energy input.
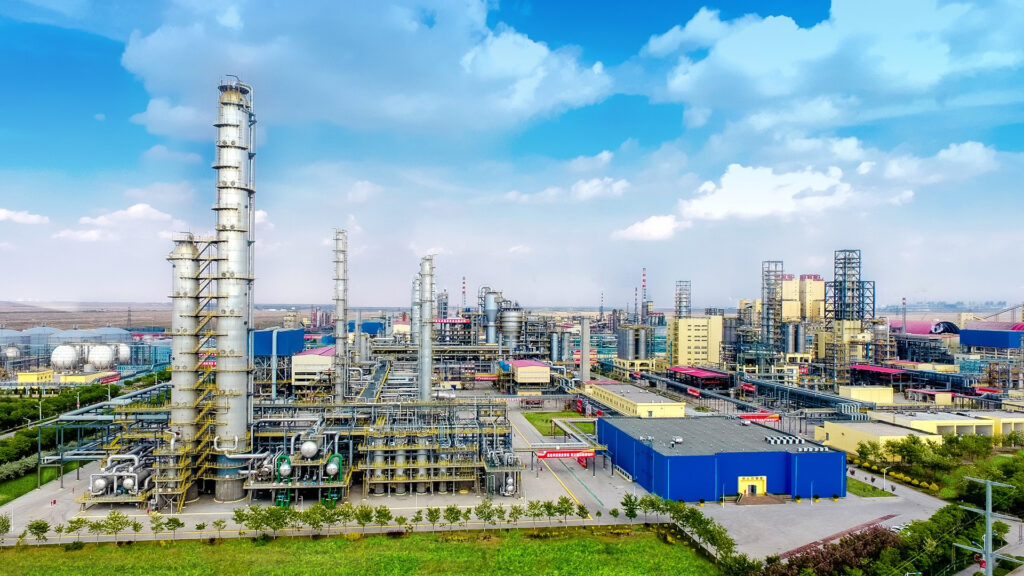
There are several options for distilling crude methanol to obtain high-grade methanol (AA Grade or IMPCA Grade), so one or more distillation columns may be needed depending on different criteria (operational costs, amount of byproducts, investment costs, final use of methanol for the chemical industry or as fuel).
We recommend listening to Episode 69 of our podcast: Renewable Methanol with Diego Clemente (CETAER HUB) to complement this information from a successful professional in methanol project development.
Don’t forget that at AtlantHy, we work daily on methanol development projects with great success throughout our history. Both in consulting and engineering as well as in handling subsidy applications.
Feel free to contact us to launch your renewable methanol project!
If you liked this article, stay tuned to keep learning in the second part, where we’ll talk about the great market opportunity for this molecule, as well as the figures involved in a methanol plant, both in terms of consumption and investment… Follow us at AtlantHy Academy!
References
IEA. (2019). The Future of Hydrogen. París.
IRENA & Methanol Institute. (2021). Innovation Outlook : Renewable Methanol.
IRENA. (2021). Renewable Methanol Outlook.
Nieminen, H. (2019). CO2 Hydrogenation to Methanol by a Liquid-Phase Process with Alcoholic Solvents: A Techno-Economic Analysis. Processes.
Sollai, S. (2023). Renewable methanol production from green hydrogen and captured CO2: A techno-economic assessment. Journal of CO2 Utilization.
Yang, Y.-N. (2022). Enhanced methanol production by two-stage reaction of CO2 hydrogenation at atmospheric pressure. Catalysis Communications.