Non-mechanical compressors
It is interesting to see how various alternatives are being explored to overcome the challenges associated with hydrogen compression. Mechanical compressors, despite their widespread use, certainly have limitations in terms of energy efficiency—particularly in low-power applications. Cryogenic storage, for instance, could be a promising option due to its higher energy density, but its viability is limited by the cost and complexity of thermal management.
Thermally driven compressors and electrochemical compressors also offer interesting prospects. The former make use of thermal energy for compression, which could improve efficiency compared to mechanical compressors. Meanwhile, electrochemical compressors may offer a more efficient and potentially more sustainable solution by using electrochemical reactions to achieve compression.
Let’s talk about each of them!
Types of non-mechanical compressors
Cryocompressors
Cryocompression appears to be an interesting strategy for addressing the challenges of both hydrogen liquefaction and compression. By combining liquefaction and compression, it takes advantage of the benefits of both storage methods. Instead of compressing hydrogen in its gaseous state, it involves pressurising liquid hydrogen at very low temperatures. This increases storage density while reducing the amount of energy required for compression, since the volumetric energy density of liquid hydrogen is significantly higher than that of gaseous hydrogen at atmospheric pressure.
Typical cryocompression systems include a pressure vessel integrated within a carbon fibre shell to minimise heat transfer between the cold liquid hydrogen and the external environment. This approach can offer an efficient and safe solution for hydrogen storage in various applications. Such vessels present two clear advantages: lower hydrogen losses due to evaporation and smaller vacuum spaces—in other words, they allow for the storage of more fuel.
They operate as follows: liquid hydrogen is transported through vacuum-insulated pipes using a cryogenic pump, and then brought to the desired pressure by means of the cryopump. Afterwards, vaporisers can convert the liquid hydrogen into high-pressure gaseous hydrogen. This process facilitates the distribution and storage of hydrogen by taking advantage of its properties in the liquid state to increase storage density and reduce the energy required for compression.
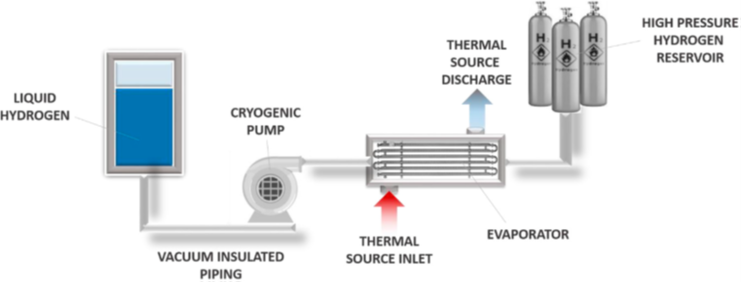
Illustration 1. Operating diagram of a cryogenic compression system (Sdanghi, 2019).
Metal hydride compressors
Metal hydride compressors offer an efficient way to compress hydrogen without relying on moving parts such as solid pistons, liquids, or diaphragms. These compressors take advantage of the properties of certain metals, alloys, or intermetallic compounds that have the ability to absorb and desorb hydrogen through heat and mass transfer within the reaction system.
The design of a metal hydride compressor includes a narrow central channel for distributing hydrogen within the reactor, as well as an annular space between this channel and the tank wall where the metal hydride is housed. When low-pressure hydrogen is introduced into the metal hydride tank through the central channel, it diffuses into the metal hydride bed, triggering an exothermic absorption process. This absorption begins at low temperatures and continues until the equilibrium pressure reaches the supply pressure level.
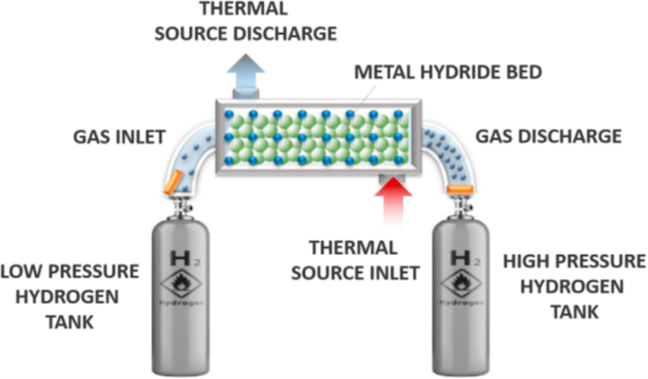
Illustration 2. Operating diagram of metal hydride compression (Sdanghi, 2019).
Electrochemical compressors
It is based on the same fundamental principles as a proton exchange membrane fuel cell (PEMFC). In this configuration, low-pressure hydrogen is introduced at the anode of the electrochemical cell. There, the hydrogen is split into protons and electrons according to the following reaction (Ströbel R, 2022):
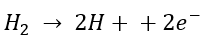
The protons travel electrochemically through a solid polymer electrolyte, known as the membrane, while the electrons follow an external path through the electrical circuit, driven by the potential difference applied to the system. When the protons and electrons reach the cathode, they recombine to form hydrogen molecules once again, resulting in an increase in pressure. These compressors are characterised by lower energy consumption and offer vibration-free operation with no moving parts.
Adsorption compressors
It operates through changes in the system’s temperature, without the need for moving mechanical components. This type of compressor can be described as a thermodynamic engine, where compression is controlled by heat transfers between the compression vessel and the system’s surroundings.
In this process, low-pressure hydrogen is introduced into a sealed tank containing a solid bed made of a porous material with a high surface area and, therefore, a high adsorption potential. Under specific temperature and pressure conditions, adsorption occurs exclusively on the surface of the porous material. Heat is then supplied to the system, resulting in a temperature increase that triggers the desorption of hydrogen. As a result, the density of the bulk hydrogen phase increases, and high-pressure hydrogen is obtained.
This method is not yet commercially developed.
Conclusion
As you will have seen, hydrogen compression technologies can be classified into two categories: mechanical and non-mechanical. Mechanical alternatives are the most widely used and are well-established, mature technologies; whereas non-mechanical options are more novel and still emerging. What is beyond doubt, however, is that compression is essential for achieving high storage densities and enabling the use of hydrogen in industrial applications.
We recommend listening to Episode 58 of our podcast: Hydrogen Compressors with Javier Cuevas (Burckhardt Compression) to complement this information.
Don’t miss any of the latest posts from AtlantHy Academy!
References
Sdanghi, G. (2019). Review of the current technologies and performances of hydrogen compression for stationary and automotive applications. Renewable and Sustainable Energy Reviews.
Ströbel R, O. M. (2022). The compression of hydrogen in an electrochemical cell based on a PE fuel cell design. Power Sources.