In the context of the energy transition and the fight against climate change, carbon capture is emerging as a key solution for reducing industrial CO₂ emissions. Among the main post-combustion carbon capture technologies, chemical solvents stand out for their technological maturity, while cryogenics is gaining ground thanks to its high energy efficiency and its ability to deliver CO₂ in liquid form, ready for storage or commercial use.
However, as discussed in previous articles, there is no one-size-fits-all technology. The technical and economic viability of each capture system depends on multiple variables: flue gas pressure, thermal and electrical energy costs, the desired CO₂ capture rate, and even the geographic location of the plant. Each of these factors can decisively affect the competitiveness of one solution over another.
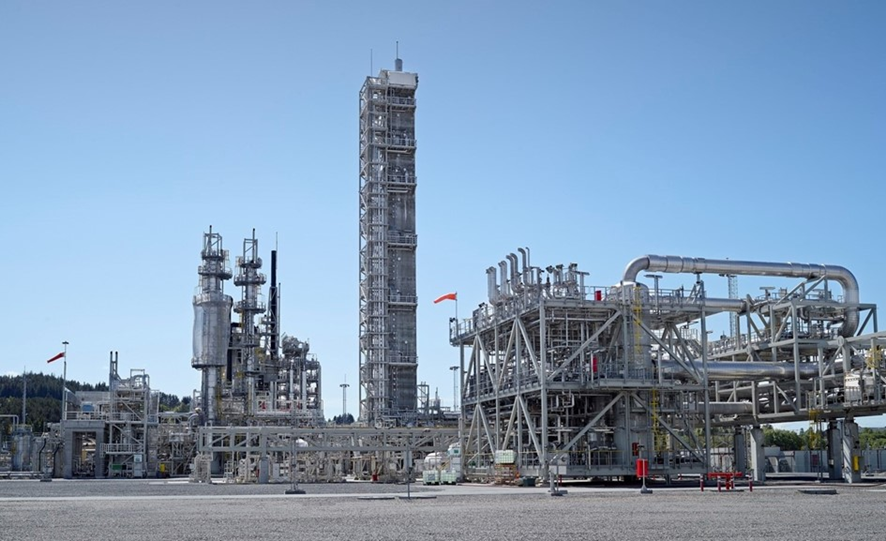
Illustration 1. CO₂ capture pilot plant in Mongstad, where different technology providers test their solvents to assess their capture efficiency (Renewable Carbon, 2021)
Throughout this article, we will delve into the main parameters that influence the cost of carbon capture, analyzing how they affect the efficiency, scalability, and profitability of the various technologies available on the market.
Capture cost vs. avoided CO₂ cost
One of the fundamental aspects when analyzing the economics of carbon capture is to distinguish between the CO₂ capture cost and the avoided CO₂ cost. Although both are commonly expressed in euros per ton, they represent different metrics. The capture cost refers to the total annualized expenditure of a plant divided by the total amount of CO₂ captured. On the other hand, the avoided CO₂ cost takes into account net emissions, also considering the CO₂ generated during the operation of the capture system, such as the consumption of thermal or electrical energy.
This second metric provides a more accurate view of the real climate impact of the process, as it reflects not only what is captured, but what is effectively prevented from being emitted into the atmosphere. Therefore, when assessing the efficiency of a carbon capture technology, it is advisable to analyze both indicators.
What determines the cost of capturing CO₂?
Talking about carbon capture means diving into a technical and economic balance between the initial investment and the operating costs over time. The cost of CO₂ capture is usually classified into two main components: CAPEX (capital expenditures), which includes design, engineering, equipment, and plant construction; and OPEX (operational expenditures), which covers energy consumption, maintenance, chemical solvent replacement, personnel, and other recurring expenses.
The selected carbon capture technology directly influences not only the technical performance of the system, but also its energy efficiency, sensitivity to energy price fluctuations, and its ability to integrate with different industrial processes. Choosing the right technology for each case is key to achieving cost-effective, scalable, and sustainable CO₂ capture.
Among the main post-combustion carbon capture technologies, chemical solvent-based systems stand out, particularly those using amines such as MEA (monoethanolamine), along with cryogenic processes. Each option offers specific advantages and limitations depending on the type of industry and operating conditions. In the case of amines, one of the most relevant factors is their high demand for low-pressure steam for solvent regeneration, which can represent between 60% and 70% of the plant’s total energy OPEX.
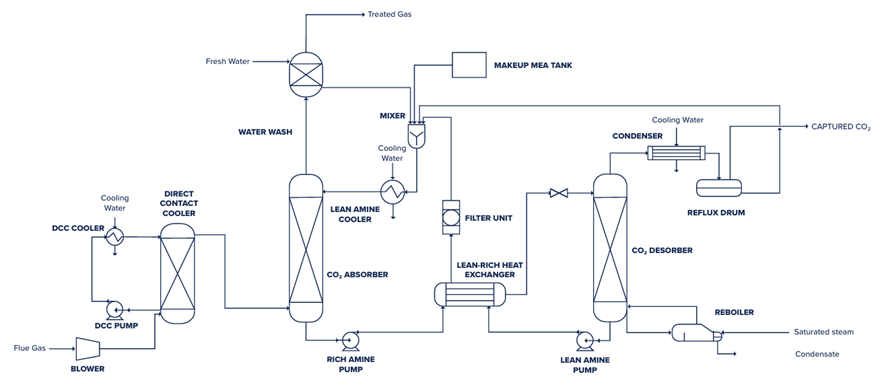
Illustration 2. Generic diagram of a CO₂ capture plant using amines (Global CCS Institute, 2025)
Cryogenic CO₂ capture, on the other hand, uses electricity to cool and condense the gas, enabling the direct recovery of liquefied CO₂ ready for geological storage or transport without requiring additional compression or liquefaction processes. Energy price sensitivity is a key factor in technology selection: if electricity is cheap, cryogenics becomes more competitive; if, instead, steam is available at low cost or comes from an existing industrial process, chemical amines may prove more economically efficient.
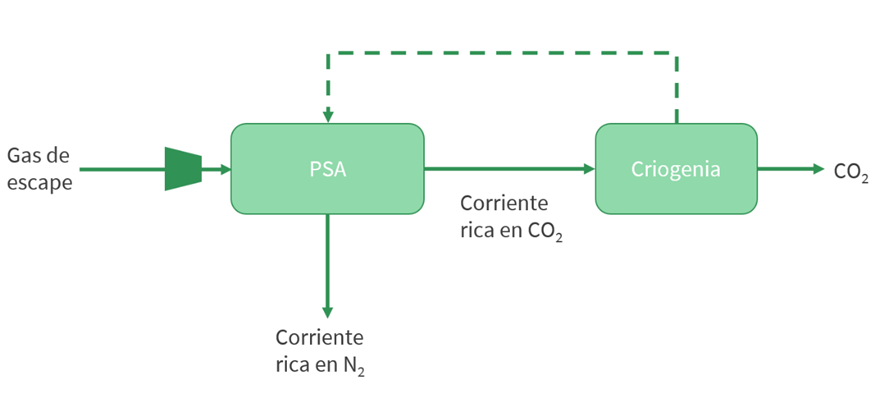
Illustration 3. General diagram of the CO₂ capture process using PSA + cryogenics (own elaboration)
Therefore, the economic evaluation of CO₂ capture technologies must always be contextual, taking into account the energy and operational conditions of each specific project.
Operating costs in a carbon capture plant vary depending on the technology used. In systems with chemical amines such as MEA (monoethanolamine), the majority of the OPEX is associated with solvent regeneration, which requires low-pressure steam. This process consumes both thermal and electrical energy to heat the solvent, operate pumps, blowers, and maintain cooling systems such as the DCC (Direct Contact Cooler). In this technology, heat consumption ranges between 0.6 – 0.9 MWh/t CO₂ and auxiliary electricity consumption is in the range of 50 – 100 kWh/t CO₂.
Factors such as the solvent composition, CO₂ concentration, and chemical binding strength influence energy consumption. Additionally, both water and amine must be periodically replenished due to thermal degradation and the presence of contaminants in flue gases.
In parallel, cryogenic CO₂ capture technology presents a different profile: it is a fully electric process, where compressors represent the main energy consumption. Its competitive advantage lies in the fact that it delivers CO₂ already liquefied, avoiding the additional compression or liquefaction steps required in solvent-based systems. Although its consumption ranges between 300 – 410 kWh per ton of CO₂, this includes the energy needed to liquefy the gas, which may be more efficient in certain industrial applications.
Both technologies also require covering fixed costs such as personnel, maintenance, insurance, and taxes, regardless of the volume captured.
Comparison between CAPEX and OPEX
In facilities that use chemical amines such as MEA, the units with the greatest weight in the CAPEX include the absorber, the water wash tower, the DCC (Direct Contact Cooler), and the flue gas blower. These components require significant dimensions to treat large volumes of gas without compromising the efficiency of the process.
On the other hand, the OPEX is dominated by:
- The consumption of steam in the reboiler to regenerate the solvent.
- The use of electricity for blowers and pumps.
- The operation of the cooling systems needed to dissipate heat at different stages of the cycle.
In fact, the reboiler represents the highest annual operating cost due to the high thermal energy demand. This has driven the development of alternatives such as mechanical vapor recompression (MVR) or heat pumps, aiming to reduce this energy burden.
During the design phase, technological decisions always seek a balance between CAPEX and OPEX. For example, operating at higher pressure in the absorber can reduce its size and lower capital investment, but at the cost of higher OPEX due to the increased energy input required. It is also common to opt for taller columns, which improve capture efficiency and reduce solvent consumption, although they require greater initial investment.
The use of modular plants helps simplify installation and shorten timelines, but demands careful integration with existing infrastructure, ensuring compatibility in inlets, outlets, and auxiliary services.

Illustration 4. Modular amine-based capture system from Carbon Clean using rotating absorbers (Carbon Clean, 2024)
To illustrate how CAPEX and OPEX are distributed within the total capture cost, one can consider a plant with a capacity to capture 1 million tonnes of CO₂ per year and an average capture efficiency of 90% (a value commonly used in the industry). The included graphs show how the costs are divided and how they vary depending on design and operational decisions.
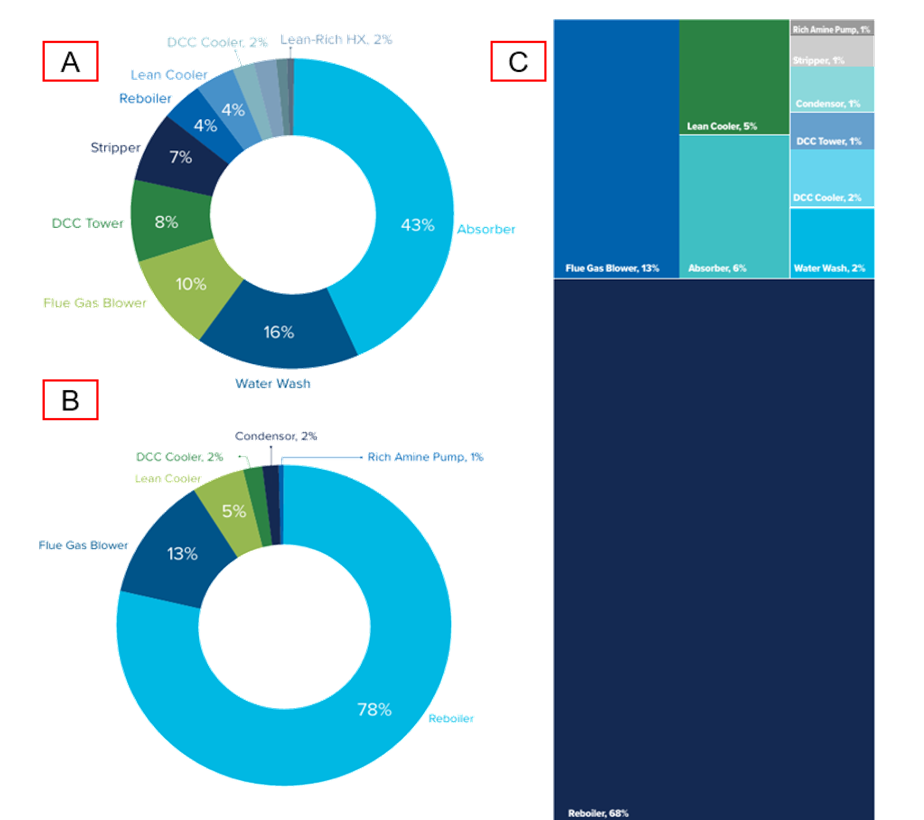
Illustration 5. Investment costs (a), operational costs (b), and annualised unit costs (c), including both CAPEX and OPEX for a 90% capture case (Global CCS Institute, 2025)1
- Estimated cost is €78 per tonne of CO₂. ↩︎
Main parameters determining capture cost
The total cost of carbon capture depends on a series of technical, energy-related and logistical parameters. Both the initial investment (CAPEX) and the operational costs (OPEX) are influenced by the plant design, the chosen technology and the site conditions.
Partial pressure of CO₂
The partial pressure of CO₂ directly affects equipment size, energy consumption, and capture process efficiency. The higher the CO₂ concentration in the input stream, the easier and cheaper it is to capture. This reduces the gas volume to be treated, allowing for more compact equipment and lower investment.
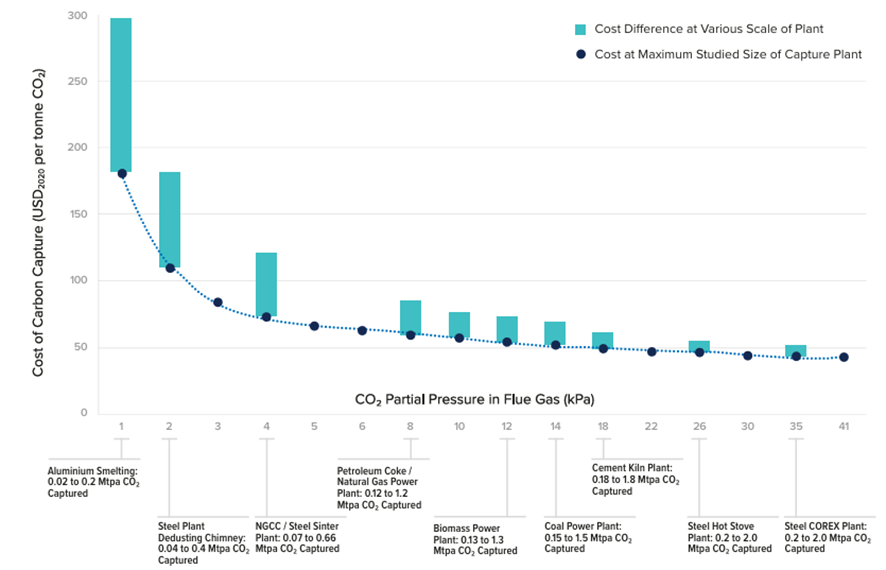
Illustration 6. Impact of partial pressure on CO₂ capture cost (Global CCS Institute, 2025)
Economies of scale
As capture capacity increases, the unit cost per tonne of CO₂ decreases. This reduction is due to the fact that the main components do not increase their cost proportionally. To estimate this effect, a common formula used in process engineering is:

Where “n” ranges between 0.6 and 0.8, depending on the type of process and technical configuration. This model is useful for preliminary estimates, although it presents some uncertainty. Nevertheless, it clearly shows how scaling up the capacity of a carbon capture plant can significantly improve its economic profitability, especially when complemented with detailed design and accurate modelling.
Capture technology
The selected technology directly impacts costs. Amines perform better at low pressures, while technologies such as membranes, cryogenics or physical solvents are more efficient at higher pressures. The use of advanced solvents can improve efficiency, although at a higher unit cost. Furthermore, mature technologies present lower risk and economic uncertainty compared to emerging ones.
Capture rate
Although it is technically possible to capture up to 99% of CO₂, costs increase non-linearly as higher efficiency is pursued. For this reason, many plants operate around 90–95%, where the cost per tonne captured remains competitive without oversizing equipment or excessively increasing energy consumption.
Energy consumption
Thermal and electrical energy consumption is one of the key factors in OPEX. Amine-based plants require large amounts of steam to regenerate the solvent, whereas cryogenic and membrane systems rely more heavily on electricity supply. If internal thermal energy is not available, additional boilers will need to be installed, increasing operational costs.
Cooling systems
Dissipating the heat generated during carbon capture requires cooling towers, seawater use, or air coolers. The choice of system depends on the local availability of water and space. In areas with water scarcity, more complex solutions can significantly increase system costs.
Flue gas pretreatment
Contaminants such as sulfur oxides (SOₓ) or nitrogen oxides (NOₓ) can degrade the solvents used, increasing replacement and maintenance costs. Efficient pretreatment reduces chemical degradation, improves system durability, and lowers long-term OPEX.
Plant location
The geographical location influences multiple variables: energy prices, labor costs, infrastructure access, space availability, and industrial integration. Installing a plant in a greenfield environment is often more cost-effective than in existing facilities (brownfield), where technical, legal, and physical constraints may exist.
Cost reduction and optimization strategies
The economic viability of a carbon capture plant depends not only on the technology used but also on how it is designed, built, and integrated into its industrial environment. Several strategies can reduce both CAPEX and OPEX, enhancing the profitability of the process without compromising its efficiency.
Economies of scale
One of the most effective ways to reduce the cost per ton of captured CO₂ is by increasing the scale of the project. The larger the capture volume, the lower the relative weight of the initial investment, since many of the core equipment components do not scale linearly with capacity. Furthermore, clustering several nearby CO₂ sources allows shared infrastructure for compression and transport, optimizing overall resource use. However, there are physical limitations—such as the maximum diameter of absorbers—that constrain the unlimited expansion of these facilities.
Modularization and standardization
Modularization has emerged as an effective solution to accelerate the deployment of capture plants, reduce risk, and simplify engineering. By manufacturing prefabricated carbon capture units in series, savings are achieved in design, assembly, and logistics. Companies like Carbon Clean and SLB Capturi have led the development of modular solutions that also enable greater automation and remote control, helping reduce operating and maintenance costs.
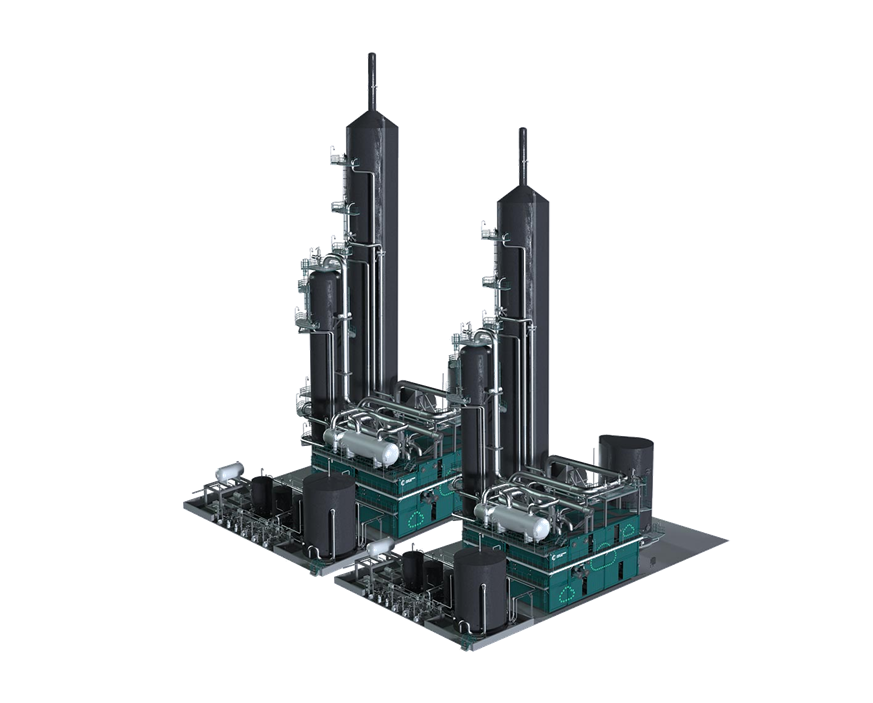
Illustration 7. Overview of the modular CO₂ capture system by the SLB Capturi, Joint Venture (SLB Capturi, 2024)
Thermal integration and cheaper energy sources
The regeneration of amine-based solvents demands substantial thermal energy. A key strategy to reduce steam consumption is to harness waste heat from existing industrial processes. This approach has been implemented, for example, at the Brevik cement plant (Heidelberg Materials), where the CO₂ capture system was designed to operate using excess thermal energy. This integration eliminated the need for additional steam generation units and significantly reduced the plant’s operating expenses (OPEX).
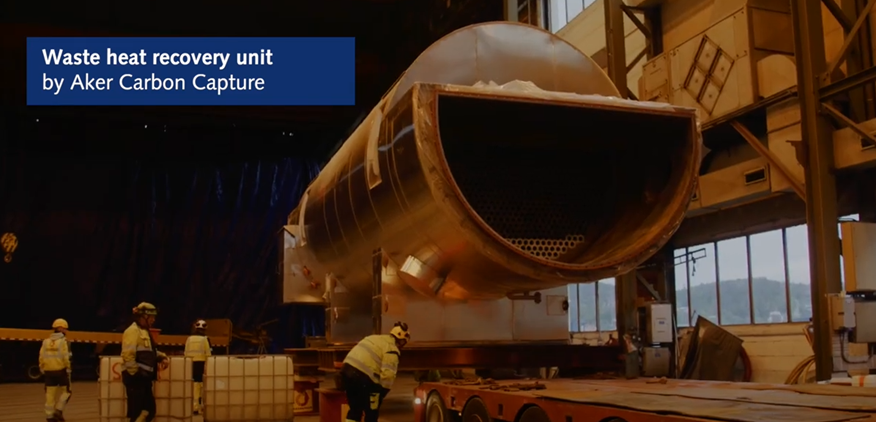
Illustration 8. Waste heat steam generation unit before delivery to the Brevik plant (Heidelberg Materials, 2024)
More affordable construction materials
Construction materials have a direct impact on CAPEX. Although stainless steel is commonly used due to its corrosion resistance, its high cost makes it a significant investment factor. Alternatives such as carbon steel or even reinforced concrete can be used in specific sections of the system without compromising durability. A notable example is the SaskPower project, where a concrete absorber was employed, significantly lowering the capital investment required.
Furthermore, the adoption of less corrosive solvents can reduce the need for highly resistant materials, resulting in cheaper equipment manufacturing and lower long-term maintenance costs.
Innovations and improvements in the capture process
Although carbon capture using amines typically follows a standardized design, multiple optimisation strategies have been developed in recent years to improve energy efficiency, reduce vapour consumption and minimise operational costs.
Key innovations include:
- Thermal exchange in the absorber: Cooling the liquid within the column during the absorption phase enhances performance, although it requires increased investment in heat exchangers and pumping systems.
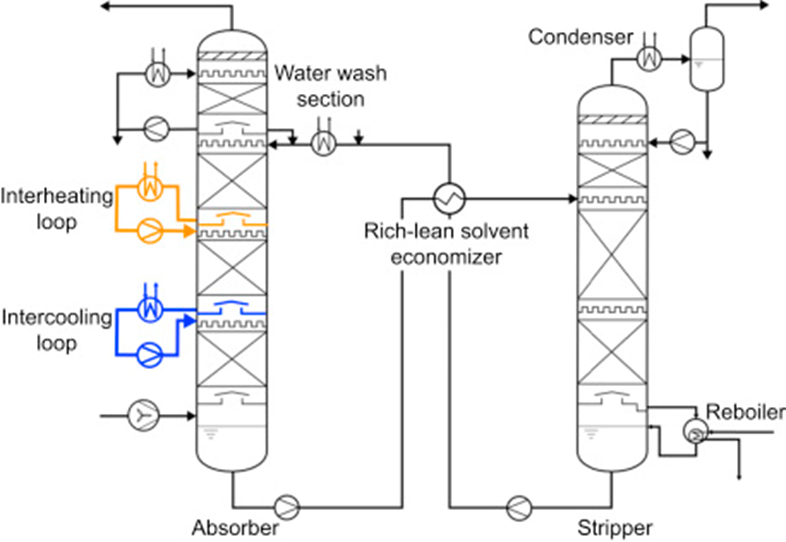
Illustration 9. Diagram of amine-based capture using heat exchange loops between absorption beds (Y. Le Moullec & T. Neveux, 2016)
- Split of the CO₂-rich solvent: Separating the stream into two parts (one preheated and the other not) optimises the thermal profile of the desorber, reducing energy consumption.
- Mechanical vapour recompression (MVR): Recovers part of the vapour from the regenerated solvent and reintegrates it into the desorber, decreasing the need for thermal energy in the reboiler.
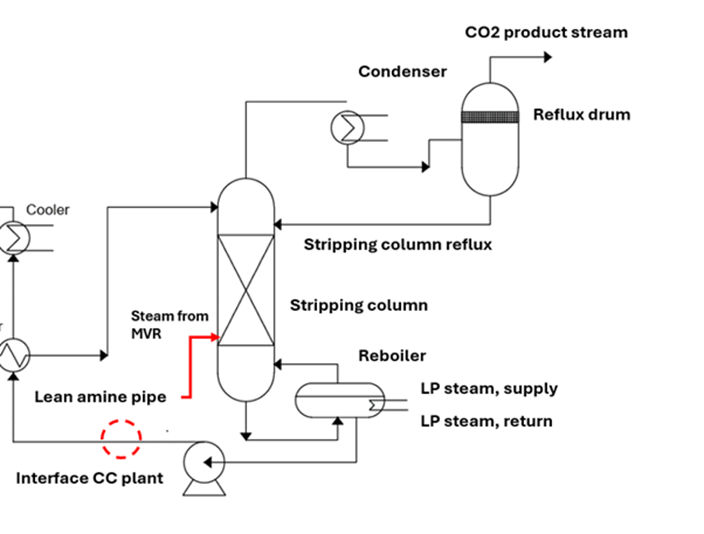
Illustration 10. Point at which MVR is applied in a capture plant (own elaboration)
- Compact rotating beds: Solutions such as those developed by Carbon Clean enhance mass transfer through rotational acceleration, reducing the size and footprint of the equipment.
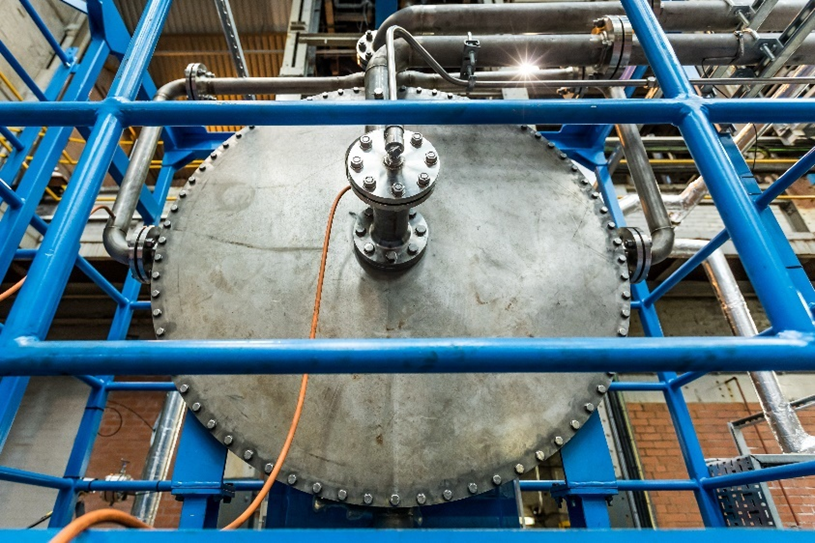
Illustration 11. Carbon Clean’s rotating bed (Cyclone cc) (Carbon Clean, 2021)
- High-pressure desorbers: Increasing the pressure helps to reduce the subsequent electricity consumption needed to compress the captured CO₂, facilitating its transport or storage.
In addition to equipment improvements, there are also adjustments in the upstream industrial process that can enhance the performance of carbon capture:
- Increasing the concentration of CO₂ in flue gases—by reducing air leaks or using oxy-combustion—improves system efficiency and reduces the overall flow to be treated.
- Reducing impurities such as NOₓ and SOₓ simplifies gas pretreatment, lowers reagent consumption and improves solvent stability.
However, any process modification must be evaluated based on technical and economic criteria. If the cost of implementing such changes outweighs the savings achieved in the capture stage, the measure may not be financially viable.
Conclusion
Carbon capture is one of the most relevant tools for reducing CO₂ emissions in the industrial sector. Its success will depend on the ability to implement efficient and economically competitive technologies tailored to each specific context. Optimising both CAPEX and OPEX, taking advantage of thermal integration, and applying technological innovations are fundamental strategies to move towards industrial plants with competitively reduced net emissions. As regulatory and societal pressure continues to grow, carbon capture will become an essential component of any industrial business strategy.
At AtlantHy, we support companies in assessing all these aspects to ensure the success of their carbon capture projects.
Don’t hesitate to contact us to make the most of your CO₂ emissions!
References
Air Liquide. (2024). PEM electrolyzers to produce renewable hydrogen: how does it work? Retrieved from https://www.airliquide.com/stories/hydrogen/pem-electrolyzers-produce-renewable-hydrogen-how-does-it-work
Air Products. (2024). Liquid Oxygen. Retrieved from https://www.airproducts.com/gases/liquid-oxygen
Carbon Clean. (2021). Carbon Clean launches breakthrough industrial carbon capture solution. Retrieved from https://www.carbonclean.com/en/press-releases/breakthrough-industrial-carbon-capture-solution
Carbon Clean. (2024). Carbon Clean announces fully columnless carbon capture, with launch of CycloneCC C1 series. Retrieved from https://www.carbonclean.com/en/press-releases/c1-launch
Doug Palfreyman, Aaron Cottrell, Peter Scaife & Louis Wibberley. (2006). TECHNO-ECONOMICS OF OXYGEN-FIRED PF POWER GENERATION WITH CO2 CAPTURE. Retrieved from https://www.researchgate.net/publication/238079799_TECHNO-ECONOMICS_OF_OXYGEN-FIRED_PF_POWER_GENERATION_WITH_CO2_CAPTURE?enrichId=rgreq-5c8be06cf66f7508efbb35f1d84c9caf-XXX&enrichSource=Y292ZXJQYWdlOzIzODA3OTc5OTtBUzoxMzQyMTIwMzIxNDMzNjBAMTQwOTAxMDA1MDQ2M
Global CCS Institute. (2025). ADVANCEMENTS IN CCS TECHNOLOGIES AND COSTS.
Heidelberg Materials. (2024). Brevik CCS Episode 3. Retrieved from https://www.youtube.com/watch?v=sbdGu2POuJE
Omega Air. (2024). Nitrogen and oxygen production. Retrieved from https://www.omega-air.si/news/news/nitrogen-and-oxygen-production
Renewable Carbon. (2021). Mitsubishi Heavy Industries Engineering to test carbon capture technology at Technology Centre Mongstad in Norway. Retrieved from https://renewable-carbon.eu/news/mitsubishi-heavy-industries-engineering-to-test-carbon-capture-technology-at-technology-centre-mongstad-in-norway/
SIAD. (2025). Oxygen Compressors. Retrieved from https://www.siadmi.com/oxygen-compressor
SLB Capturi. (2024). SLB and Aker Carbon Capture joint venture awarded FEED contract by CO280 for large-scale carbon removal project. Retrieved from https://www.slb.com/news-and-insights/newsroom/press-release/2024/slb-and-aker-joint-venture-awarded-feed-contract-by-co280-for-large-scale-carbon-removal-project
Y. Le Moullec & T. Neveux. (2016). Process modifications for CO2 capture. Absorption-Based Post-combustion Capture of Carbon Dioxide.
J. Franson, THE CANADIAN PRESS. (06/11/2015). Quest carbon capture and storage facility in Fort Saskatchewan Alta. Retrieved from https://climateinstitute.ca/safe-bets-wild-cards/carbon-capture-in-canada/ (Imagen de portada)