Did you know that ammonia (NH₃) will be a key element enabling us not only to use hydrogen in the chemical sector or maritime transport, but also to transport it over thousands of kilometres?
In this article, the AtlantHy team shares some of the essential insights into this molecule.
Introduction and context
First of all, it’s important to highlight that ammonia is one of the seven basic chemicals—alongside ethylene, propylene, methanol, and the BTX aromatics (benzene, toluene, and xylene)—used to produce all other chemicals. It is the second most widely produced chemical compound by mass after sulphuric acid, with an annual output of 183 million tonnes. Around four-fifths of all ammonia is used to manufacture nitrogen-based fertilisers such as urea and ammonium nitrate; in this role, it supports food production for roughly half of the world’s population (IRENA, 2022).
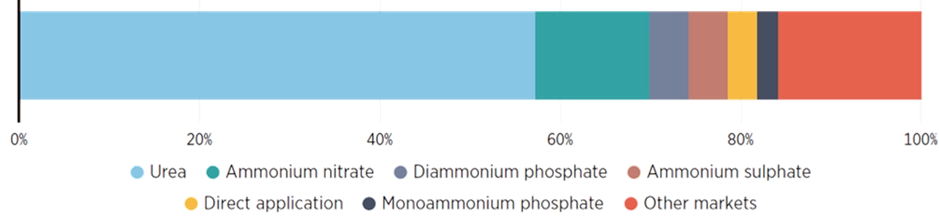
Global ammonia production amounts to 183 MtNH₃/year (IRENA, 2022) and currently accounts for around 2% (8.6 EJ) of total final energy consumption. Just over 70% of ammonia is produced via steam methane reforming (SMR) of natural gas, while most of the remaining capacity relies on coal gasification. This results in a natural gas demand of 170 bcm (equivalent to 20% of industrial natural gas consumption) and a coal demand of 75 Mtce, representing 5% of industrial coal use (IEA, 2021).
All of this means that CO₂ emissions from ammonia production today are extremely high—reaching nearly 500 MtCO₂ per year, which is roughly equivalent to the annual emissions of a country like South Africa, just to put it into perspective.
Decarbonising the ammonia sector is already a major challenge in itself, given the enormous potential impact. However, the role of this molecule will not be limited to these sectors in the coming years. Since NH₃ does not emit CO₂ when burned, it could serve as a clean fuel to deliver energy to end users without producing greenhouse gas emissions during its consumption.
The challenge, therefore, lies in producing ammonia with minimal emissions associated with its generation—this means moving away from fossil-based feedstocks and making the leap towards what is known as renewable or low-carbon ammonia, as we’ll explore next.
If this becomes a reality, ammonia will be in a strong position to expand into new sectors—such as maritime transport and power generation in combined-cycle plants. These two sectors have a massive impact on the energy system and require energy carriers that are both chemically stable over time and energy-dense, in order to store energy for long periods and in confined spaces (such as a ship’s fuel tank).
If this transition takes place, projections for ammonia consumption in the coming years are extremely promising—with production expected to triple by 2050, as shown in the following image:
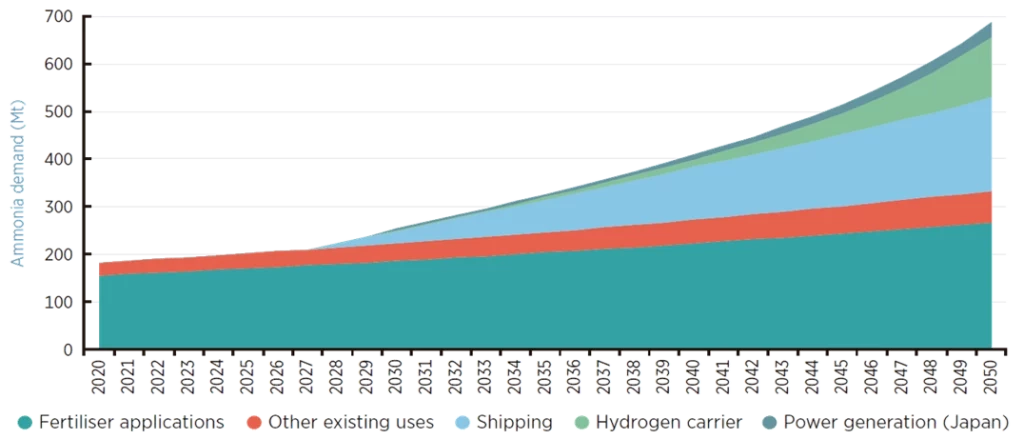
So, the key to ammonia becoming a central player in decarbonisation lies in its renewable origin—but… how do we achieve that?
Well, keep reading…
Renewable ammonia production process
NH₃ is a colourless gas with a strong, unpleasant odour. It is slightly flammable and not classified as toxic, but it can cause asphyxiation if inhaled, making it highly dangerous if not handled with care. Moreover, due to its higher density compared to air, any leak can result in low-lying gas clouds at ground level, which can be extremely hazardous.
In addition, ammonia has a relatively low energy density (18.8 MJ/kg) compared to fossil fuels such as natural gas. However, it can be easily liquefied—either at 8 bar at ambient temperature or at –33°C under atmospheric pressure—making it a very dense and manageable molecule in terms of storage and transport.
Ammonia production is one of the first industrial processes to have been developed on a large scale, and its implementation made the population growth of the last century possible (Rouwenhorst, 2021).
The Birkeland–Eyde process was one of the first methods used for industrial-scale ammonia production, developed in 1903. It relied on an electric arc to convert nitrogen, oxygen, and water into nitric acid. However, it was extremely energy-intensive, requiring around 400 GJ per tonne of NH₃. Just ten years later, the Haber–Bosch process was implemented at scale and quickly became the dominant production method. During the First World War, the Haber–Bosch process underwent significant development as a means to produce munitions and explosives. By the 1930s, it had already become the primary method for producing ammonia—a role it continues to play today (IRENA, 2022).
In the early decades of industrial fertiliser production, electrolysis powered by hydroelectric energy was commonly used. Coal gasification was another early source of hydrogen. During the 1960s and 1970s, the increased availability of competitively priced natural gas led to a wider adoption of steam methane reforming (SMR) for hydrogen production, due to its lower overall production costs. As a result, most electrolysis-based plants eventually shut down.
The Haber–Bosch ammonia synthesis process operates in the same way regardless of the hydrogen source.

Ammonia synthesis, an exothermic process that releases 0.7 MWh per tonne of NH₃, requires high temperatures (400–650 °C) and pressures (100–400 bar) in the presence of iron-based catalysts. This catalyst accelerates the reaction sufficiently to make the process economically viable for industrial production, keeping both the catalyst mass and the equipment size within reasonable limits (Modak, 2022). Most of the required energy comes from the reaction itself, although some electricity is consumed—around 0.64 MWh per tonne of NH₃—to operate equipment such as motors and pumps, as well as the air separation unit needed to supply nitrogen (Ikaheimo, 2018).
In the production process, highly purified nitrogen and hydrogen streams are fed into a synthesis reactor. Because the reaction is an equilibrium process, full conversion is not achieved. Therefore, the outlet stream is cooled to condense and separate the produced ammonia, while the unreacted gases are recirculated to increase overall conversion. The system includes a gas–liquid separator and a purge stream to remove inerts; hydrogen is recovered from the purge using membranes to minimise losses. For the ammonia to be considered renewable, both the hydrogen and nitrogen must be sourced from water electrolysis powered by renewable electricity (IRENA, 2022).
After the reaction, ammonia is separated from nitrogen and hydrogen using a condenser.
This production system is illustrated below:
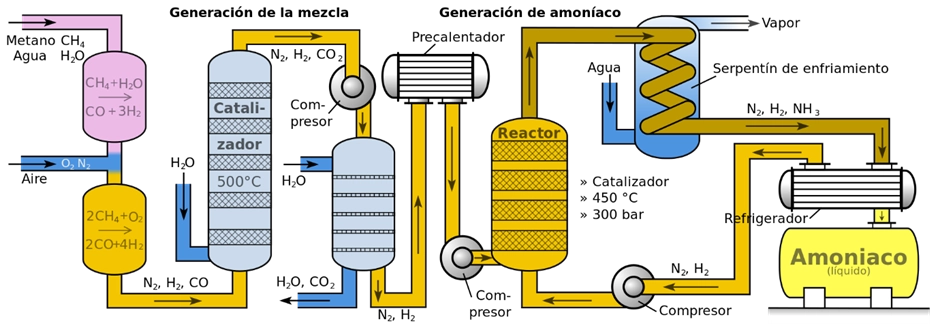
Renewable ammonia
As mentioned earlier, ammonia is produced by combining hydrogen and nitrogen. The difference between the conventional and renewable routes lies in the source of the hydrogen: traditionally, it is derived from natural gas or coal, whereas in renewable scenarios, it is generated using electrolysers.
However, although the production process remains the same, there are numerous challenges when it comes to sizing an ammonia plant that sources its hydrogen from electrolysis.
The most significant challenge is how to overcome the intermittency of renewable energy sources. The reactors used in the Haber–Bosch process are exothermic systems that generate their own reaction heat. When the supply of H₂ and N₂ to the reactor falls below a certain threshold, the heat produced is no longer sufficient to sustain the reaction at the required production rates, causing the process to stop.
Therefore, it is necessary to link the power supply to the electrolyser in compliance with the delegated acts and the RED III Directive, while ensuring sufficient hydrogen storage to allow the ammonia production process remains as stable as possible. This not only requires in-depth analysis by engineering and design teams, but also involves high capital investment in equipment.
These additional costs, combined with the higher production price of renewable hydrogen compared to fossil-based hydrogen, mean that the value (€/tonne) of renewable or green ammonia is still significantly higher than that of its conventional counterpart. However, as shown in the following graph, this gap is expected to narrow by 2050—mainly due to the falling cost of renewable hydrogen production, as we will explore in other AtlantHy articles.
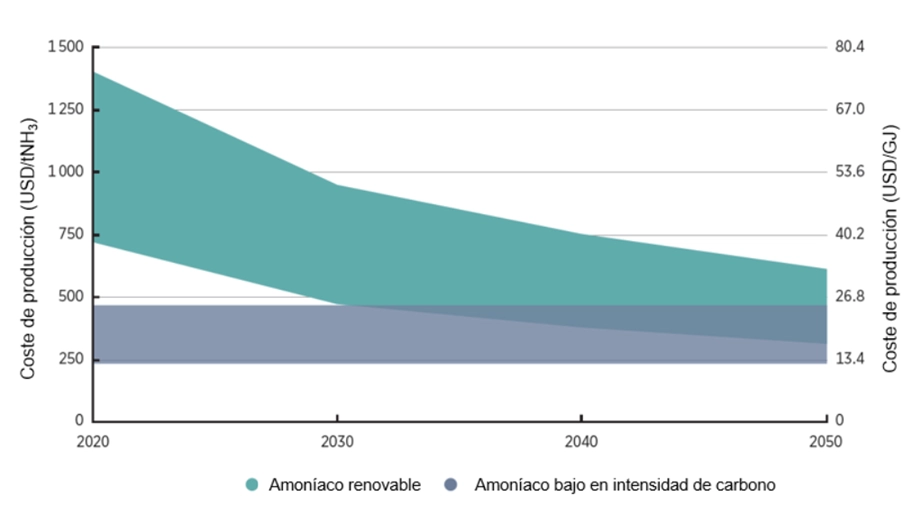
One advantage of renewable ammonia projects is that they can be implemented using existing infrastructure. This is evident in most of the projects announced so far, which are making use of operational ammonia plants to begin introducing small amounts of renewable hydrogen relative to the total hydrogen consumption.
We must not forget that the RED III directive sets minimum consumption targets of 42.5% renewable hydrogen for industry by 2030, which could result in significant hydrogen demand in this sector towards the end of the decade. However, the fertiliser industry still faces uncertainty as to whether this regulation directly applies to it.
Conclusions
Renewable ammonia will play a key role in the decarbonisation of energy systems. Its role is now well understood—what remains is to deploy projects that deliver this molecule to end users.
In addition, its ability to transport hydrogen at low cost will make it possible to harness distant resources—such as wind energy from South America or solar power from Australia—and deliver them to consumer economies.
As a result, renewable ammonia plants are expected to expand rapidly in the coming years.
At AtlantHy, we support companies not only with feasibility analysis and engineering for the development of this type of plant, but also with modelling to ensure full compliance with all applicable regulations—including delegated acts, certification schemes, and the RED III directive.
Don’t hesitate to get in touch—let’s get your renewable ammonia project off the ground!
References
A Valera-Medinaa, H. X.-J. (2018). Ammonia for power. Progress in Energy and Combustion Science , 63-102.
Abdullah Emre Yüzbasıoglu, C. A. (2022). The current situation in the use of ammonia as a sustainable energy source and its industrial potential. Current Research in Green and Sustainable Chemistry, 5.
IEA . (2021). IEA 50. Retrieved from Ammonia Technology Roadmap: https://www.iea.org/reports/ammonia-technology-roadmap
IEA. (2021). Ammonia Technology Roadmap. Paris.
Ikaheimo, J. (2018). Power-to-ammonia in future North European 100 % renewable power and heat system. International Journal of Hydrogen Energy, 17295-17308.
IRENA . (2022). GLOBAL HYDROGEN TRADE TO MEET THE 1.5ºC CLIMATE GOAL: Part I. Abu Dhabi.
IRENA. (2022). Innovation Outlook Renewable Ammonia. Abu Dhabi.
Matthew J. Palys, H. W. (9 de Diciembre de 2020). Renewable ammonia for sustainable energy and agriculture: Vision and systems engineering opportunities. Department of Chemical Engineering and Materials Science, págs. 1-5.
Matz, M. (Marzo de 2022). The Breakthrough Potential of Green Ammonia. Business & Technology Surveillance, págs. 1-11.
Modak, J. M. (2022). Haber process for ammonia synthesis. Reson , 69–77.
Opeyemi A. Ojelade, S. F.-J. (2023). Green ammonia production technologies: A review of practical progress . Journal of Environmental Management , 17.
Rouwenhorst, K. H. (2021). 1921–2021: A Century of Renewable Ammonia Synthesis. MDPI.