The aviation world is changing—and so is the way we fly, with cleaner and more sustainable solutions on the horizon. As emissions continue to rise and environmental regulations become increasingly stringent, Sustainable Aviation Fuel (SAF) is emerging as the leading solution for a greener sky. Whether driven by strict quotas set by authorities or the growing environmental awareness of passengers, the reality is that the aviation sector is under immediate pressure to shift towards renewable fuels in order to reduce the emissions associated with its flights.
In this AtlantHy Academy article, we will discuss the production of synthetic aviation fuel from renewable hydrogen.
Introduction to synthetic SAF
In 2022, aviation was responsible for emitting approximately 800 Mt of CO₂, accounting for 2% of global energy-related CO₂ emissions. It has also shown a faster growth rate in emissions over recent decades than rail, road, or maritime transport (IEA, 2024).
To align the sector with decarbonisation goals, emission reduction targets have been established through the implementation of the ReFuelEU Aviation regulation at the European level. This regulation sets a minimum share of sustainable aviation fuel (SAF) consumption of up to 70% by 2050 at EU airports (Illustration 1).
This is reflected in concrete production targets for sustainable aviation fuel set out in the latest approved update of the Renewable Energy Directive (RED III), which establishes minimum consumption levels of Renewable Fuels of Non-Biological Origin (RFNBOs) across various transport sectors, including aviation.
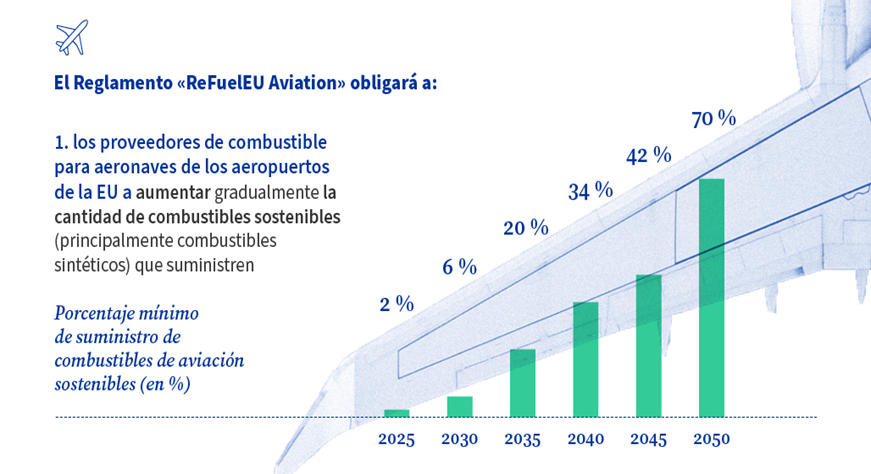
Illustration 1 Sustainable fuel consumption obligations under the ReFuelEU Aviation Regulation (European Council, 2024)
These obligations refer to the total share of sustainable aviation fuel, with a smaller target specifically for synthetic fuel (produced from electrolytic hydrogen). In this case, the targets for 2030, 2035, 2040, and 2050 are set at 1.2%, 5%, 15%, and 35%, respectively. Meeting these targets will require an enormous scale-up, as kerosene consumption in Europe is close to 50 million tonnes. If fully replaced with synthetic fuel derived from hydrogen and CO₂, this would require around 25 million tonnes of hydrogen—or approximately 250 GW of electrolysis capacity.
Aviation fuel—commonly known as kerosene—is, like petrol or diesel, a mixture of different hydrocarbons traditionally derived from crude oil in refineries. It can be compared with its fossil-based counterparts, as shown in the following image:
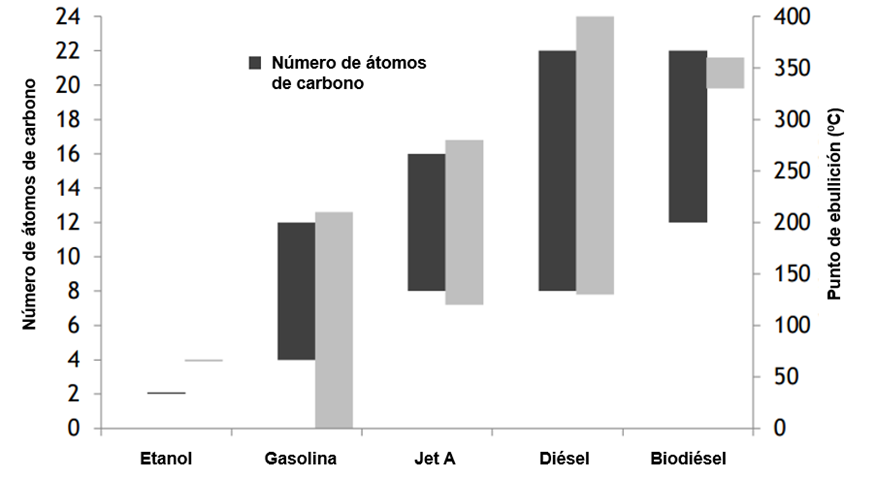
Illustration 2 Boiling point ranges and number of carbon atoms in different fuels (Susan van Dyk, 2021)
Due to the high energy density required for flight, integrating renewable energy sources into the aviation sector poses significant challenges. Direct electrification or the use of hydrogen is currently not a viable solution. As a result, it becomes essential to develop a sustainable fuel capable of replacing conventional kerosene while maintaining similar properties.
This renewable fuel can be produced either from bio-based feedstocks (biofuels) or from renewable hydrogen obtained via electrolysis and carbon dioxide emissions, following the Power-to-X approach to produce an RFNBO-compliant fuel aligned with the RED III framework. In the latter case, the resulting kerosene is referred to as e-kerosene, as it is derived from renewable hydrogen through electrolysis and considered an electrofuel.
Because this fuel is highly similar to conventionally produced kerosene, it can be used within the existing infrastructure, enabling faster adoption of sustainable technologies in the aviation sector and avoiding the need for investment in new aircraft fleets or equipment.
SAF Production Process
The following technologies are currently the main pathways for producing Sustainable Aviation Fuel (SAF):
- Biomass gasification followed by Fischer-Tropsch synthesis.
- Pyrolysis or hydrothermal liquefaction of biomass followed by hydrotreatment.
- Biomass gasification followed by methanol synthesis and subsequent SAF production.
- Fermentation of sugars to produce alcohols such as ethanol or isobutanol, followed by alcohol-to-jet conversion (Alcohol-to-Jet, AtJ).
- Hydroprocessing of vegetable or animal oils and fats.
- Production of renewable hydrogen and capture of biogenic CO₂, conversion into a hydrogen and carbon monoxide mixture, followed by Fischer-Tropsch synthesis (Power-to-Liquids route).
- Production of renewable hydrogen and capture of biogenic CO₂, synthesis of synthetic methanol and subsequent conversion to SAF.
With regard to renewable hydrogen, the two relevant production routes are the last two, both of which use carbon dioxide as the carbon source and either follow the Fischer–Tropsch synthesis pathway or use synthetic methanol (e-methanol) as an intermediate for SAF production.
In terms of compatibility with current infrastructure, only the Fischer–Tropsch route for SAF production is currently approved by the American Society for Testing and Materials (ASTM). The methanol-based pathway has not yet received approval, although it is expected to be certified in the near future (by mid or late 2024).
As for the outputs of the SAF production process, it is important to note that the yield is not 100%. A certain fraction of gasoline-range hydrocarbons (naphtha), diesel, and light gases are also produced as by-products. These compounds can be valorised and/or reused within the SAF production process itself to increase overall yields or reduce external energy input.
Fischer–Tropsch synthesis from hydrogen and carbon dioxide
The SAF production process via Fischer–Tropsch starts from CO₂ and hydrogen and is divided into two main stages:
- Reverse Water Gas Shift to produce synthesis gas from CO₂ and hydrogen
- Fischer–Tropsch synthesis of heavy hydrocarbons, followed by purification and upgrading through hydrotreatment and hydrocracking
In the first stage, the Reverse Water Gas Shift process is used to convert carbon dioxide (CO₂) and hydrogen (H₂) into a mixture of hydrogen and carbon monoxide (CO), known as synthesis gas or syngas, which can then be used for hydrocarbon synthesis. It is worth noting that this technology (RWGS) is not yet proven at commercial scale, making it a critical step for improvement in order to enable broader deployment of this route. Once syngas is produced, it can be fed into the conventional Fischer–Tropsch (F-T) process.
Fischer–Tropsch synthesis for SAF production is a catalytic process in which synthesis gas (CO and H₂) is converted, in the presence of iron-based catalysts, into a petroleum-like product known as Fischer–Tropsch crude. This crude can then be easily processed to produce a wide range of liquid hydrocarbons, including kerosene. The process was first developed in the 1920s and is considered a mature technology, named after its inventors Franz Fischer and Hans Tropsch (ETIP Bioenergy, 2021).
The appearance of the reactors used in the F–T process is shown in Illustration 3. The reactors pictured correspond to the Fischer–Tropsch units built by MAN for Shell’s Pearl GTL (Gas-to-Liquids) project in Qatar.
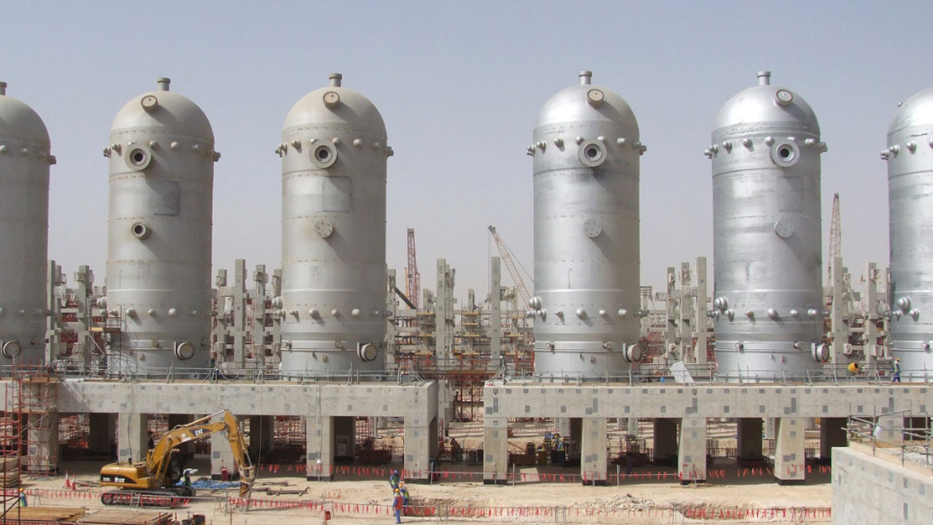
Illustration 3 Fischer–Tropsch reactors (MAN, 2024)
To increase the yield of liquid fuels such as naphtha and SAF, the resulting product stream is subjected to hydrotreatment and hydrocracking (upgrading processes), in which hydrogen is consumed to break down heavier fractions into lighter hydrocarbons within the boiling range of SAF or naphtha. Finally, the upgraded products go through a fractionation step to isolate a SAF stream that meets the required specifications for use as aviation fuel.
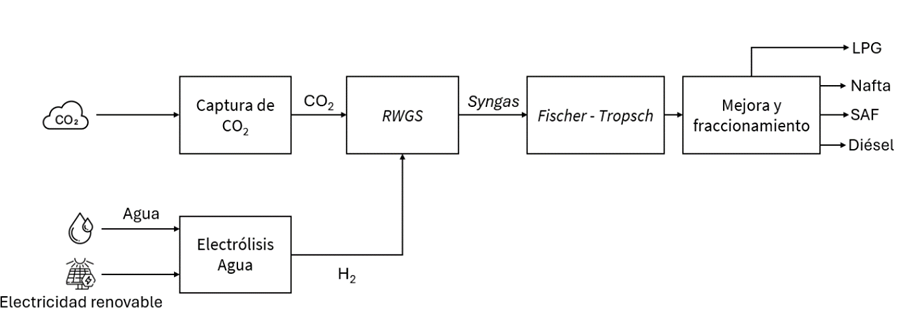
Illustration 4 General process diagram for SAF production from CO₂ and renewable hydrogen
Synthetic methanol production and subsequent processing into SAF
In the methanol-based route (methanol-to-kerosene or methanol-to-jet), three main stages are required:
- Methanol production and purification.
- Conversion of methanol to olefins.
- Oligomerisation and fractionation to produce SAF.
In this process, hydrogen and carbon dioxide are combined in a hydrogenation reaction to synthesise methanol. The methanol is then used to produce light olefins such as ethylene or propylene through the Methanol-to-Olefins (MTO) process. Finally, the resulting olefins undergo oligomerisation to form heavier hydrocarbons within the boiling range of aviation fuel. This step is combined with hydrogenation to ensure that the final product meets the required specifications for aviation use.
As with the F–T process, the methanol route requires a final fractionation step to separate the various product streams and produce a SAF stream that complies with aviation fuel standards.
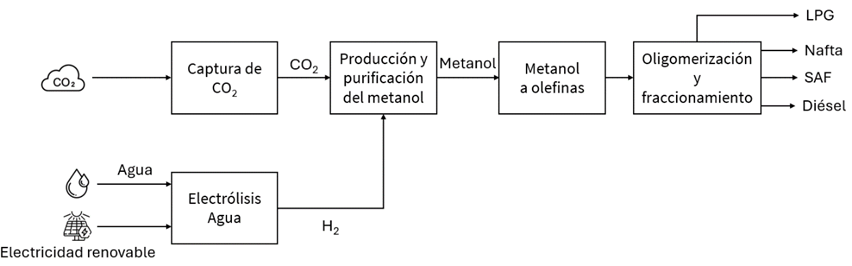
Illustration 5 Methanol-to-kerosene process diagram
While the methanol-to-olefins process is proven at commercial scale—with significant deployment in China for the subsequent production of plastics—the methanol-to-kerosene route is at a lower level of technological maturity and has not yet been implemented commercially. However, the process builds on commercially proven technology used for the production of synthetic gasoline.
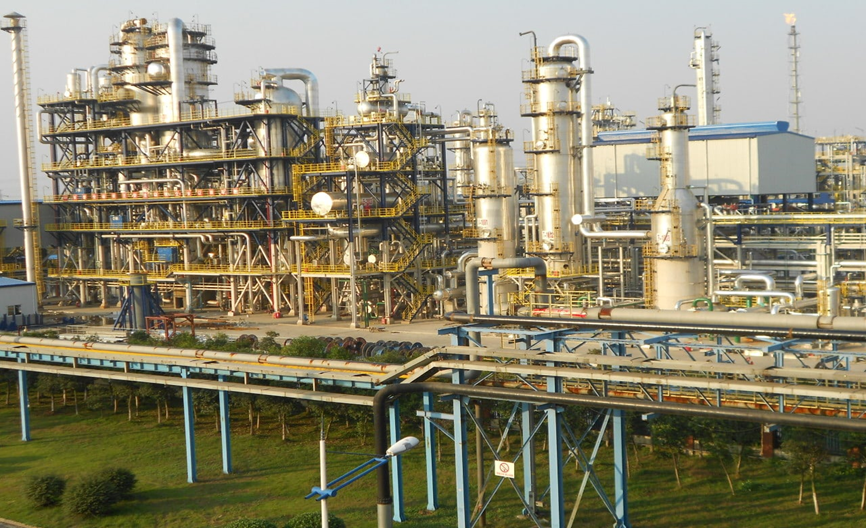
Illustration 6 Honeywell UOP MTO production unit (Chemical Engineering, 2018)
Comparison between the Fischer–Tropsch and Methanol-to-SAF routes
Both production pathways show strong potential to meet the growing demand for sustainable aviation fuel. However, they differ significantly in key aspects. In terms of kerosene yield, the methanol route offers higher selectivity, as it generates fewer by-products than the Fischer–Tropsch-based process.
On the other hand, in terms of energy efficiency, both routes achieve similar efficiency levels with respect to the calorific value of the kerosene produced. However, the methanol-based route has the advantage of operating at lower temperatures compared to the Fischer–Tropsch process, since the RWGS stage in the F–T route requires temperatures of up to 950 °C.
Lastly, process flexibility is another factor to consider. The Fischer–Tropsch route requires a larger production capacity and is better suited to large-scale projects. Moreover, it is less compatible with decentralised production models, which could otherwise take advantage of low-cost hydrogen generation in regions with abundant renewable resources and then transport it to a centralised SAF facility.
In this regard, the methanol-to-SAF process offers greater compatibility with renewable energy-based systems. Since methanol is a liquid, it can be produced in a decentralised manner in locations where production costs are competitive, and then transported to a centralised SAF facility.
The lower flexibility of the F–T route could limit the short-term deployment of this technology, as it would require large-scale renewable hydrogen plants and CO₂ sources—something that is currently difficult to achieve. In contrast, the methanol route benefits from the possibility of integrating several medium-scale methanol production projects into a larger SAF production scheme, without incurring significant economic penalties from transporting the methanol to the centralised facility (Bube, S., Bullerdiek, N., Voß, S., & Kaltschmitt, M., 2024).
In conclusion, both SAF production routes will play a key role in decarbonising the aviation sector. The preferred route in each case will depend on the specific characteristics of the project, as well as associated costs, required flexibility, and the technological development each pathway undergoes in the coming years.
We recommend listening to Episode 69 of our podcast: Renewable Methanol with Diego Clemente (CETAER HUB), for further insights from a successful professional in the field of methanol project development.
Don’t forget that at AtlantHy we work daily on synthetic fuel development projects, with a strong track record of success. We support initiatives at every stage—from consultancy and engineering to grant application and regulatory support.
Get in touch with us to launch your SAF project based on hydrogen and carbon capture!
If you found this article useful, stay tuned for the second part, where we’ll explore the major market opportunity for this molecule, along with key figures related to SAF plant development—covering both consumption and investment needs… Follow us on AtlantHy Academy!
References
Bube, S., Bullerdiek, N., Voß, S., & Kaltschmitt, M. (2024). Kerosene production from power-based syngas – A technical comparison of the Fischer-Tropsch and methanol pathway. Fuel.
Chemical Engineering. (2018). World’s largest single-train methanol-to-olefins plant now operating. Retrieved from https://www.chemengonline.com/worlds-largest-single-train-methanol-to-olefins-plant-nowoperating/
ETIP Bioenergy. (2021). Fischer-Tropsch Synthesis.
European Council. (2024). Fit for 55: increasing the uptake of greener fuels in the aviation and maritime sectors. Retrieved from https://www.consilium.europa.eu/es/infographics/fit-for-55-refueleu-and-fueleu/
IEA. (2024). Aviation. Retrieved from https://www.iea.org/energy-system/transport/aviation
MAN. (Enero de 2024). Retrieved from https://www.man-es.com/process-industry/products/chemical-reactors/water–air–oil-operated-reactors
Susan van Dyk, J. S. (2021). Progress in Commercialization of Biojet/Sustainable Aviation Fuels (SAF): Technologies, potential and challenges.